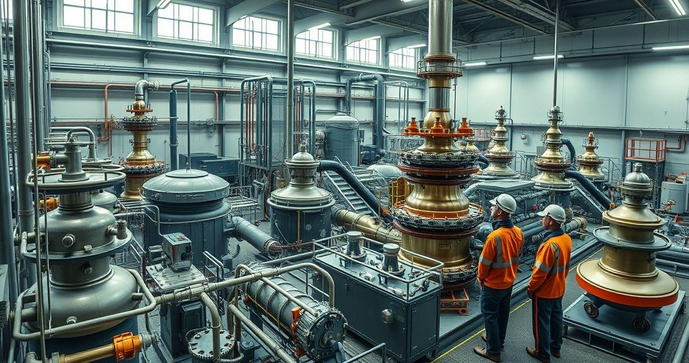
Saiba sobre Reatores químicos industriais: Como escolher o melhor para sua fábrica
Tipos de reatores químicos industriais e suas aplicações
Os reatores químicos industriais são fundamentais para a transformação de matérias-primas em produtos desejados. Existem vários tipos de reatores, cada um com características específicas que os tornam adequados para diferentes aplicações.
Um dos tipos mais comuns é o reator batch, também conhecido como reator descontínuo. Ele é utilizado em processos onde a produção ocorre em lotes, permitindo maior flexibilidade na operação. Frequentemente, esse tipo é aplicado na indústria farmacêutica e na produção de produtos químicos especiais, onde a variação na produção é necessária.
Outro tipo é o reator contínuo, ideal para processos de produção de grande escala. Esses reatores permitem uma operação constante, o que resulta em uma produção mais eficiente. Eles são amplamente utilizados na indústria petroquímica e na fabricação de polímeros, onde grandes volumes são essenciais.
Os reatores de tanque agitado são um modelo popular, que combina diferentes processos químicos. Seu design permite uma mistura homogênea dos reagentes, sendo muito utilizados em biotecnologia e em operações suspensas. Isso facilita reações onde a homogeneidade é crucial para a eficiência do processo.
Os reatores tubulares, por outro lado, são projetados para fluxos contínuos de reagentes por um tubo. Eles são excelentes para reações rápidas e são frequentemente usados na indústria de gás e na produção de produtos químicos baseados em petróleo. Esse tipo de reator maximiza a área de superfície para a transferência de calor e massa.
Por fim, o reator de leito fixo é ideal para reações catalíticas que exigem uma fase sólida. Muito utilizado na indústria química para a produção de combustíveis e na purificação de gases, ele oferece uma alta eficiência na conversão de reagentes.
A escolha do tipo de reator deve levar em consideração fatores como o tipo de reação, as condições operacionais e os requisitos do produto final. Avaliar as necessidades específicas de cada processo garantirá a implementação do reator mais adequado.
Critérios para seleção de reatores em processos químicos
A seleção de um reator para processos químicos é uma decisão crítica que impacta a eficiência e a qualidade da produção. Diversos critérios devem ser considerados para garantir que o reator escolhido atenda às necessidades específicas da operação.
Um dos principais critérios é a natureza da reação química. Reações exotérmicas, que liberam calor, podem exigir reatores com sistemas de controle térmico eficientes, enquanto reações endotérmicas, que absorvem calor, necessitam de um fornecimento constante de energia. O entendimento do tipo de reação ajudará a determinar a configuração do reator.
Outro fator importante é a escala de produção. Para pequenas produções ou produtos personalizados, reatores batch podem ser mais adequados, enquanto para grandes volumes, reatores contínuos são preferíveis. A escolha deve alinhar a capacidade do reator às demandas de produção.
A viscosidade do fluido também deve ser considerada. Fluidos de alta viscosidade podem dificultar o transporte e a mistura, exigindo reatores que ofereçam capacidades específicas, como agitação mais intensa ou design tubular. O tipo de agitação necessário pode influenciar diretamente a seleção do reator.
Adicionalmente, a compatibilidade dos materiais de construção do reator com os reagentes é crucial. Materiais reativos podem corroer o reator ou contaminar o produto final, portanto, é essencial utilizar materiais resistentes e apropriados, como aço inoxidável ou materiais poliméricos, para a construção do reator.
O controle de parâmetros operacionais, como pressão e temperatura, também é um elemento decisivo. Reatores que operam em condições extremas de temperatura ou pressão precisam ser projetados especificamente para essas exigências, garantindo segurança e eficácia durante o processo.
Por fim, o custo de investimento e operação deve ser avaliado. A escolha do reator deve considerar não apenas os custos iniciais de implementação, mas também as despesas contínuas com manutenção e operação. Um reator mais eficiente pode se justificar financeiramente ao longo do tempo, oferecendo retornos melhores.
Vantagens dos reatores contínuos versus reatores descontínuos
A comparação entre reatores contínuos e descontínuos é essencial na hora de decidir o melhor sistema para processos químicos. Cada tipo oferece vantagens que podem influenciar a eficiência, a qualidade do produto e os custos operacionais.
Os reatores contínuos são conhecidos pela sua operação ininterrupta, o que resulta em uma maior eficiência de produção. Eles são ideais para processos que exigem produção em larga escala, pois permitem um fluxo constante de reagentes e produtos. Isso reduz o tempo de espera entre as etapas de produção, otimizando o processo total.
Uma das principais vantagens dos reatores contínuos é a uniformidade na qualidade do produto final. Como o fluxo é constante e as condições operacionais são estáveis, há uma menor variabilidade entre os lotes produzidos, o que é fundamental em indústrias onde a consistência é crucial, como na farmacêutica ou alimentícia.
Em contrapartida, os reatores descontínuos, ou batch, oferecem flexibilidade na produção. Eles permitem a realização de diferentes reações em um único equipamento, tornando-os adequados para a produção de pequenos lotes ou produtos personalizados. Essa versatilidade é vantajosa em mercados onde a demanda por variações de produtos pode mudar rapidamente.
Outro ponto a favor dos reatores descontínuos é que eles geralmente requerem um investimento inicial menor em comparação aos contínuos. A simplicidade do design e a recarga de matérias-primas em lotes tornam esses reatores mais acessíveis para empresas de menor porte ou em fases iniciais de desenvolvimentos.
Entretanto, os reatores contínuos tendem a ter menores custos de operação a longo prazo devido à sua eficiência. A capacidade de operar 24 horas por dia aumenta a produção e reduz a necessidade de mão de obra, pois há menos paradas para recarga e limpeza entre os lotes.
Diante disso, a escolha entre reatores contínuos e descontínuos deve considerar não apenas a escala de produção, mas também a flexibilidade necessária, o controle de qualidade, os custos iniciais e operacionais, e a natureza das reações que serão realizadas. Analisar essas variáveis ajudará as empresas a tomarem decisões informadas sobre o sistema de reatores mais adequado.
Avaliação de materiais para a construção de reatores
A escolha dos materiais para a construção de reatores químicos é uma etapa fundamental que impacta diretamente a performance, a durabilidade e a segurança do equipamento. A avaliação adequada dos materiais garante que o reator funcione de maneira eficaz durante todo o ciclo de vida.
Um dos fatores mais importantes na seleção de materiais é a compatibilidade química. O material deve ser capaz de suportar os reagentes e as condições operacionais sem sofrer corrosão, degradação ou contaminação. Por exemplo, ácidos fortes e agentes oxidantes exigem materiais como aço inoxidável, titânio ou ligas especiais que resistam a ataques corrosivos.
Além da resistência química, a resistência à temperatura é outro critério essencial. Reações químicas podem gerar calor excessivo, e os materiais utilizados devem suportar essas elevações sem sofrer deformações ou perda de integridade. Materiais como cerâmicas e alguns polímeros podem ser adequados para altas temperaturas, enquanto os metais devem ser selecionados com base em suas propriedades térmicas.
Outro aspecto a considerar na avaliação de materiais é a resistência à pressão. Reatores que operam sob pressões elevadas devem ser construídos com materiais que suportem essas condições sem falhas estruturais. A espessura das paredes, o tipo de soldagem e a forma como o reator é projetado são essenciais para garantir a segurança em operações pressurizadas.
A facilidade de fabricação e montagem dos materiais também deve ser levada em conta. Certos materiais podem ser mais difíceis de cortar, molde ou soldar, o que pode impactar os custos e o tempo de construção do reator. A seleção de materiais que sejam fáceis de trabalhar pode resultar em economias significativas durante a fabricação.
Por fim, a análise de custos é um critério decisivo na escolha dos materiais. Embora seja tentador optar por soluções mais baratas, é fundamental equilibrar o custo com a qualidade e a durabilidade. Materiais de baixo custo podem resultar em maiores gastos com manutenção e reparos no futuro, enquanto a escolha de materiais de alta resistência pode minimizar custos a longo prazo.
Em resumo, a avaliação de materiais para a construção de reatores químicos deve considerar a compatibilidade química, a resistência à temperatura e pressão, a facilidade de fabricação e os custos associados. Um processo de seleção cuidadoso garantirá um reator seguro, eficiente e de longa durabilidade, otimizado para as necessidades específicas de produção.
Impacto da temperatura e pressão no desempenho do reator
A temperatura e a pressão são fatores cruciais que influenciam diretamente o desempenho dos reatores químicos. A adequação dessas variáveis afeta a intensidade e a velocidade das reações químicas, sendo essencial para otimizar a eficiência do processo.
A temperatura afeta as taxas de reação química de acordo com a Lei de Arrhenius, que indica que, com o aumento da temperatura, a energia cinética das moléculas aumenta, resultando em mais colisões eficazes entre reagentes. Esse aumento na taxa de reação pode levar a um aumento na produtividade, mas também pode provocar riscos, como a formação de subprodutos indesejáveis. Portanto, um controle preciso da temperatura é fundamental para maximizar a eficiência do processo.
Além disso, cada reação química possui uma temperatura ideal onde a eficiência é maximizada e a formação de subprodutos é minimizada. Reatores que operam fora dessas condições ideais podem apresentar problemas, como baixo rendimento e aumento de custos operacionais. Portanto, dispositivos de controle de temperatura, como trocadores de calor, são frequentemente utilizados para manter as condições adequadas.
A pressão, por sua vez, também desempenha um papel crítico, especialmente em reações que envolvem gases. Aumentar a pressão geralmente resulta em maior densidade de reagentes, o que eleva a taxa de colisões entre moléculas, acelerando a reação. Esse princípio é particularmente relevante em reações de equilíbrio, onde mudanças na pressão podem deslocar o equilíbrio para favorecer a formação de produtos desejados.
No entanto, a operação em altas pressões requer o uso de materiais resistentes e um design robusto do reator para garantir a segurança. Reatores mal projetados podem sofrer falhas catastróficas sob pressão excessiva, tornando essencial que os engenheiros estejam atentos às especificações do projeto.
Ainda, a temperatura e a pressão podem interagir de maneiras complexas durante as reações químicas. Em muitos casos, o aumento da temperatura pode exigir uma alteração na pressão para manter o desempenho do reator. É fundamental, portanto, realizar simulações e testes para entender completamente como essas variáveis se comportam em conjunto.
Em suma, o impacto da temperatura e pressão no desempenho do reator é significativo e deve ser monitorado cuidadosamente. Ajustes nessas condições podem melhorar a eficiência, a segurança e a viabilidade econômica das reações químicas em processos industriais. Portanto, um controle rigoroso é imprescindível para otimizar a produção e minimizar riscos.
Tendências e inovações em reatores químicos industriais
A indústria química está em constante evolução, e as tendências e inovações em reatores químicos industriais desempenham um papel fundamental na melhoria da eficiência e na sustentabilidade dos processos de produção. Nos últimos anos, diversas inovações têm surgido para otimizar o desempenho dos reatores e atender às crescentes demandas do mercado.
Uma das principais tendências é a automação e digitalização dos processos. A implementação de tecnologias de controle avançadas, como sensores inteligentes e sistemas de monitoramento em tempo real, permite um gerenciamento mais eficiente das condições do reator. Isso não apenas melhora a consistência do produto final, mas também proporciona uma resposta rápida a qualquer desvio nas condições operacionais.
Além disso, a integração de inteligência artificial (IA) e aprendizado de máquina nas operações de reatores está em ascensão. Esses sistemas podem analisar grandes volumes de dados para otimizar condições operacionais, prever falhas e ajustar processos automaticamente. Essa capacidade preditiva permite um aumento da eficiência e uma redução de custos operacionais ao minimizar o tempo de inatividade.
A sustentabilidade também está moldando o futuro dos reatores químicos. Há uma crescente demanda por processos que minimizem o desperdício e a utilização de recursos. Isso inclui a pesquisa e desenvolvimento de reatores que favoreçam reações em condições mais brandas, reduzindo a necessidade de energia e minimizando a geração de subprodutos perigosos. Reatores que utilizam energias renováveis, como a energia solar, para operações térmicas são exemplos notáveis dessa tendência.
Outra inovação importante é o desenvolvimento de reatores modulares. Esses reatores permitem uma maior flexibilidade na produção, pois podem ser facilmente escalonados ou adaptados a diferentes produtos. Com o aumento da demanda por personalização, a capacidade de ajustar rapidamente a configuração do reator é um diferencial competitivo significativo.
Os reatores de micro- e nanomateriais também estão ganhando destaque, especialmente em aplicações farmacêuticas e de bioprocessos. Eles oferecem maior área de superfície e, portanto, podem aumentar a eficiência das reações, além de possibilitar a realização de processos em escalas menores com maior controle.
Por fim, a evolução dos materiais utilizados na construção de reatores está revolucionando o setor. Novas ligas metálicas, polímeros avançados e cerâmicas são desenvolvidos para atender a requisitos de resistência química e térmica, resultando em equipamentos mais duráveis e eficientes. Essas inovações proporcionam maior segurança e confiabilidade nas operações.
Em resumo, as tendências e inovações em reatores químicos industriais estão moldando o futuro da produção química. Com avanços em automação, sustentabilidade, modularidade e novos materiais, os reatores estão se tornando mais eficientes e adaptáveis às necessidades dinâmicas do mercado, promovendo um setor químico mais sustentável e competitivo.
A compreensão dos reatores químicos industriais e suas diversas características é essencial para otimizar processos de produção. Desde a seleção adequada de tipos de reatores até a escolha dos materiais e o controle de temperatura e pressão, cada decisão tomada impacta diretamente a eficiência, a segurança e a qualidade do produto final.
Além disso, as novas tendências e inovações trazem oportunidades significativas para a indústria, permitindo que os processos se tornem mais sustentáveis, flexíveis e eficazes. A automação e a digitalização, bem como o uso de novas tecnologias e materiais, prometem revolucionar o modo como as reações químicas são conduzidas, preparando a indústria química para os desafios do futuro.
Investir na compreensão e aplicação dessas práticas e tecnologias não só garante um aumento na competitividade, mas também prepara as empresas para atender às necessidades de um mercado em constante evolução. Portanto, a continuidade do aprendizado e da adaptação às inovações é crucial para o sucesso na indústria química.
Gostou? compartilhe!