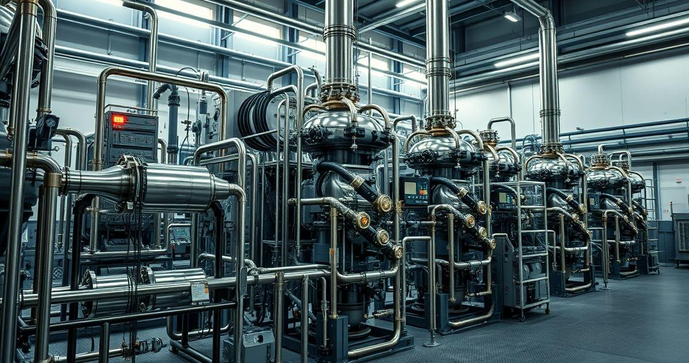
Saiba sobre Reatores Industriais: Entenda sua Importância e Aplicações na Indústria
Reatores Industriais desempenham um papel crucial na transformação de matérias-primas em produtos químicos e outros materiais essenciais. Com uma variedade de tipos e aplicações, esses equipamentos são fundamentais para a eficiência e segurança dos processos industriais. Neste artigo, exploraremos os diferentes tipos de reatores, suas vantagens, manutenção e as inovações que estão moldando o futuro da indústria.
Tipos de Reatores Industriais e Suas Aplicações
Os reatores industriais são equipamentos essenciais em diversos setores, como químico, petroquímico, farmacêutico e de alimentos. Eles são projetados para facilitar reações químicas controladas, permitindo a produção em larga escala de substâncias desejadas. A escolha do tipo de reator adequado depende de vários fatores, incluindo a natureza da reação, as propriedades dos reagentes e produtos, e as condições operacionais desejadas. A seguir, apresentamos os principais tipos de reatores industriais e suas aplicações.
1. Reatores de Batelada
Os reatores de batelada são utilizados para realizar reações em lotes, ou seja, uma quantidade específica de reagentes é processada de cada vez. Este tipo de reator é ideal para processos que não exigem produção contínua e são frequentemente utilizados em indústrias farmacêuticas e de alimentos. A flexibilidade dos reatores de batelada permite a fácil adaptação a diferentes formulações e processos, tornando-os uma escolha popular para a produção de produtos em pequena escala.
Uma das principais vantagens dos reatores de batelada é a capacidade de realizar reações complexas que podem exigir condições específicas de temperatura e pressão. Além disso, eles permitem um controle mais rigoroso sobre as condições de reação, o que é crucial em processos sensíveis, como a produção de medicamentos. No entanto, a desvantagem é que a produção em batelada pode ser menos eficiente em comparação com reatores contínuos, especialmente em operações de grande escala.
2. Reatores Contínuos
Os reatores contínuos operam de forma ininterrupta, permitindo a entrada constante de reagentes e a saída contínua de produtos. Este tipo de reator é amplamente utilizado em indústrias que requerem produção em larga escala, como a petroquímica e a produção de biocombustíveis. Os reatores contínuos são projetados para maximizar a eficiência e a produtividade, tornando-os ideais para processos que exigem grandes volumes de produção.
Uma das principais vantagens dos reatores contínuos é a redução do tempo de ciclo, uma vez que a produção não é interrompida para a troca de lotes. Isso resulta em uma maior eficiência operacional e menores custos de produção. No entanto, a desvantagem é que eles podem ser menos flexíveis em termos de adaptação a diferentes produtos ou formulações, exigindo investimentos significativos em equipamentos para mudanças de processo.
3. Reatores de Fluxo Turbulento
Os reatores de fluxo turbulento são projetados para promover uma mistura eficiente dos reagentes, resultando em uma taxa de reação mais rápida. Este tipo de reator é frequentemente utilizado em processos que envolvem reações rápidas ou exotérmicas, onde a transferência de calor e massa é crítica. Os reatores de fluxo turbulento são comuns em indústrias químicas e petroquímicas, onde a eficiência e a velocidade são essenciais.
A principal vantagem dos reatores de fluxo turbulento é a sua capacidade de promover uma mistura homogênea, o que resulta em uma taxa de reação mais alta. No entanto, eles podem exigir um controle rigoroso das condições operacionais para evitar problemas como a formação de subprodutos indesejados ou a degradação dos reagentes.
4. Reatores de Leito Fixo
Os reatores de leito fixo são utilizados em processos onde os catalisadores são imobilizados em um leito sólido, permitindo que os reagentes fluam através do leito. Este tipo de reator é amplamente utilizado em processos de catálise, como a produção de amônia e a hidrogenação de óleos. Os reatores de leito fixo são conhecidos por sua eficiência e capacidade de operar em condições de alta pressão e temperatura.
A principal vantagem dos reatores de leito fixo é a alta eficiência na conversão de reagentes, uma vez que os catalisadores permanecem em contato constante com os reagentes. No entanto, a desvantagem é que a manutenção e a limpeza do leito podem ser desafiadoras, especialmente em processos que geram depósitos ou obstruções.
5. Reatores de Leito Fluidizado
Os reatores de leito fluidizado são projetados para suspender partículas sólidas em um fluido, criando um leito que se comporta como um líquido. Este tipo de reator é amplamente utilizado em processos de combustão, pirólise e reações químicas que envolvem sólidos. Os reatores de leito fluidizado são conhecidos por sua eficiência na transferência de calor e massa, tornando-os ideais para processos que exigem uma mistura uniforme.
A principal vantagem dos reatores de leito fluidizado é a capacidade de operar em condições de alta eficiência, com uma excelente transferência de calor e massa. No entanto, eles podem ser sensíveis a variações nas condições operacionais, o que pode afetar a estabilidade do leito e a eficiência do processo.
Em resumo, a escolha do tipo de reator industrial adequado depende das características específicas do processo e dos produtos desejados. Cada tipo de reator possui suas vantagens e desvantagens, e a seleção correta pode impactar significativamente a eficiência e a rentabilidade da produção. Para garantir o funcionamento adequado dos reatores e outros equipamentos industriais, é fundamental realizar a manutenção em trocador de calor e seguir as melhores práticas de operação e manutenção.
Vantagens dos Reatores Industriais na Produção
Os reatores industriais desempenham um papel fundamental na produção de uma ampla gama de produtos químicos, farmacêuticos e alimentícios. Sua importância se reflete nas diversas vantagens que oferecem, contribuindo para a eficiência, segurança e sustentabilidade dos processos produtivos. A seguir, exploraremos as principais vantagens dos reatores industriais na produção.
1. Eficiência na Produção
Uma das principais vantagens dos reatores industriais é a eficiência que proporcionam na produção de substâncias químicas. Eles são projetados para otimizar as condições de reação, permitindo que os reagentes se transformem em produtos de forma rápida e eficaz. Isso resulta em um aumento significativo na taxa de conversão, reduzindo o tempo necessário para completar as reações e, consequentemente, aumentando a produtividade.
Além disso, os reatores industriais podem ser configurados para operar em condições ideais, como temperatura e pressão controladas, o que maximiza a eficiência das reações. Essa capacidade de otimização é especialmente importante em processos que envolvem reações complexas ou que requerem condições específicas para evitar a formação de subprodutos indesejados.
2. Flexibilidade e Adaptabilidade
Os reatores industriais oferecem uma flexibilidade considerável em termos de produção. Eles podem ser projetados para atender a diferentes tipos de reações e produtos, permitindo que as indústrias se adaptem rapidamente às mudanças nas demandas do mercado. Essa adaptabilidade é crucial em um ambiente industrial dinâmico, onde as necessidades dos consumidores podem mudar rapidamente.
Por exemplo, reatores de batelada são ideais para a produção de pequenos lotes de produtos personalizados, enquanto reatores contínuos são mais adequados para a produção em larga escala. Essa diversidade de opções permite que as empresas ajustem suas operações de acordo com as necessidades específicas de produção, garantindo que possam atender às demandas do mercado de forma eficaz.
3. Redução de Custos Operacionais
A utilização de reatores industriais pode resultar em uma redução significativa nos custos operacionais. A eficiência na produção, combinada com a capacidade de operar em condições ideais, contribui para a diminuição do consumo de energia e matérias-primas. Isso não apenas reduz os custos diretos de produção, mas também minimiza o desperdício de recursos, tornando os processos mais sustentáveis.
Além disso, a automação e o controle avançado dos reatores industriais permitem uma operação mais precisa e eficiente. Isso reduz a necessidade de intervenção manual e diminui o risco de erros operacionais, resultando em uma produção mais econômica e segura.
4. Melhoria na Qualidade do Produto
Os reatores industriais são projetados para garantir a consistência e a qualidade dos produtos finais. A capacidade de controlar as condições de reação, como temperatura, pressão e tempo, permite que as indústrias produzam substâncias com propriedades específicas e uniformes. Isso é especialmente importante em setores como o farmacêutico, onde a qualidade do produto é crítica para a segurança e eficácia dos medicamentos.
Além disso, a utilização de catalisadores em reatores industriais pode melhorar a seletividade das reações, resultando em produtos com menos impurezas e subprodutos indesejados. Essa melhoria na qualidade do produto não apenas atende às exigências regulatórias, mas também aumenta a satisfação do cliente e a reputação da marca.
5. Sustentabilidade e Redução de Impacto Ambiental
Os reatores industriais também desempenham um papel importante na promoção da sustentabilidade e na redução do impacto ambiental. A eficiência na utilização de recursos e a minimização do desperdício são aspectos fundamentais para a produção sustentável. Os reatores modernos são projetados para operar de maneira mais limpa e eficiente, reduzindo a geração de resíduos e emissões.
Além disso, muitos reatores industriais estão sendo adaptados para utilizar matérias-primas renováveis e processos mais ecológicos. Isso não apenas contribui para a sustentabilidade, mas também atende à crescente demanda por produtos ambientalmente responsáveis. A implementação de tecnologias mais limpas e eficientes é uma tendência crescente na indústria, e os reatores industriais estão na vanguarda dessa transformação.
6. Inovação e Avanços Tecnológicos
A indústria de reatores está em constante evolução, com inovações e avanços tecnológicos que melhoram ainda mais a eficiência e a eficácia dos processos. O desenvolvimento de novos materiais, designs e tecnologias de controle tem permitido a criação de reatores mais avançados e eficientes. Isso inclui a integração de sistemas de automação e monitoramento em tempo real, que permitem um controle mais preciso das condições de operação.
Essas inovações não apenas melhoram a eficiência dos reatores, mas também aumentam a segurança operacional. A capacidade de monitorar e ajustar as condições de reação em tempo real reduz o risco de acidentes e falhas, garantindo um ambiente de trabalho mais seguro para os operadores.
Em resumo, os reatores industriais oferecem uma série de vantagens significativas na produção, incluindo eficiência, flexibilidade, redução de custos, melhoria na qualidade do produto, sustentabilidade e inovação. Essas características tornam os reatores essenciais para a indústria moderna, permitindo que as empresas atendam às demandas do mercado de forma eficaz e responsável. A escolha do reator adequado e a implementação de melhores práticas operacionais são fundamentais para maximizar os benefícios desses equipamentos e garantir o sucesso a longo prazo das operações industriais.
Manutenção e Segurança em Reatores Industriais
A manutenção e a segurança em reatores industriais são aspectos cruciais para garantir a eficiência operacional e a proteção dos trabalhadores e do meio ambiente. Os reatores, sendo equipamentos complexos e frequentemente operando sob condições extremas de temperatura e pressão, exigem cuidados especiais para evitar falhas e acidentes. Neste artigo, abordaremos as melhores práticas de manutenção e as medidas de segurança necessárias para garantir o funcionamento adequado dos reatores industriais.
1. Importância da Manutenção Preventiva
A manutenção preventiva é uma abordagem proativa que visa identificar e corrigir problemas antes que eles se tornem falhas significativas. Em reatores industriais, a manutenção preventiva é essencial para garantir que todos os componentes estejam funcionando corretamente e para evitar paradas inesperadas na produção. Isso inclui a verificação regular de sistemas de controle, válvulas, bombas e outros equipamentos associados ao reator.
Além disso, a manutenção preventiva ajuda a prolongar a vida útil dos equipamentos, reduzindo os custos de reparo e substituição. A implementação de um programa de manutenção preventiva bem estruturado pode incluir inspeções regulares, limpeza de componentes, lubrificação e substituição de peças desgastadas. Essa abordagem não apenas melhora a eficiência do reator, mas também contribui para a segurança operacional.
2. Inspeções Regulares e Monitoramento
As inspeções regulares são uma parte fundamental da manutenção em reatores industriais. Elas devem ser realizadas de acordo com um cronograma estabelecido, que pode variar dependendo do tipo de reator e das condições de operação. Durante as inspeções, os técnicos devem verificar a integridade estrutural do reator, bem como o funcionamento de todos os sistemas de segurança.
O monitoramento contínuo das condições operacionais também é essencial. Isso pode incluir a instalação de sensores que medem temperatura, pressão e vazão, permitindo que os operadores detectem rapidamente quaisquer anomalias. O uso de tecnologia de monitoramento em tempo real pode ajudar a identificar problemas antes que eles se tornem críticos, permitindo uma resposta rápida e eficaz.
3. Treinamento e Capacitação da Equipe
A segurança em reatores industriais também depende do treinamento e da capacitação da equipe que opera e mantém esses equipamentos. Todos os operadores e técnicos devem receber treinamento adequado sobre os procedimentos de operação e manutenção, bem como sobre as práticas de segurança. Isso inclui o conhecimento sobre os riscos associados ao manuseio de substâncias químicas e as medidas de emergência a serem tomadas em caso de acidentes.
Além disso, a realização de simulações e exercícios práticos pode ajudar a preparar a equipe para situações de emergência. A conscientização sobre a importância da segurança e a promoção de uma cultura de segurança dentro da organização são fundamentais para minimizar riscos e garantir um ambiente de trabalho seguro.
4. Medidas de Segurança em Reatores
As medidas de segurança em reatores industriais são essenciais para proteger os trabalhadores e o meio ambiente. Isso inclui a instalação de dispositivos de segurança, como válvulas de alívio de pressão, sistemas de contenção e sensores de detecção de vazamentos. Esses dispositivos ajudam a prevenir acidentes e a mitigar os efeitos de falhas operacionais.
Além disso, é importante ter um plano de emergência bem definido, que inclua procedimentos para evacuação, contenção de vazamentos e resposta a incêndios. A realização de simulações regulares de emergência pode ajudar a garantir que todos os membros da equipe saibam como agir em caso de um incidente.
5. Documentação e Registro de Manutenção
A documentação adequada das atividades de manutenção é uma parte crucial do gerenciamento de reatores industriais. Todos os registros de manutenção, inspeções e reparos devem ser mantidos de forma organizada e acessível. Isso não apenas ajuda a garantir a conformidade com as regulamentações, mas também fornece informações valiosas para a análise de desempenho e a identificação de tendências de falhas.
Além disso, a documentação pode ser útil para auditorias e inspeções regulatórias, garantindo que a empresa esteja em conformidade com as normas de segurança e ambientais. A manutenção de registros detalhados também facilita a identificação de áreas que podem precisar de melhorias ou atualizações nos procedimentos de manutenção.
6. Integração com Outros Sistemas Industriais
A manutenção e a segurança em reatores industriais não devem ser tratadas isoladamente. A integração com outros sistemas industriais, como tanques industriais e sistemas de transporte, é fundamental para garantir uma operação segura e eficiente. A comunicação entre diferentes sistemas permite uma melhor coordenação e resposta a situações de emergência.
Além disso, a implementação de sistemas de automação e controle pode melhorar a segurança operacional, permitindo que os operadores monitorem e ajustem as condições de operação em tempo real. A automação também pode reduzir a necessidade de intervenção manual em situações potencialmente perigosas, minimizando o risco de acidentes.
Em resumo, a manutenção e a segurança em reatores industriais são aspectos essenciais para garantir a eficiência operacional e a proteção dos trabalhadores e do meio ambiente. A implementação de práticas de manutenção preventiva, inspeções regulares, treinamento da equipe e medidas de segurança adequadas são fundamentais para minimizar riscos e garantir um ambiente de trabalho seguro. A documentação adequada e a integração com outros sistemas industriais também desempenham um papel importante na gestão eficaz dos reatores. Ao priorizar a manutenção e a segurança, as indústrias podem operar de forma mais eficiente e responsável, contribuindo para a sustentabilidade e a segurança no ambiente de trabalho.
Inovações Tecnológicas em Reatores Industriais
As inovações tecnológicas em reatores industriais têm desempenhado um papel fundamental na transformação da indústria química e em outros setores que dependem de processos de reação controlados. Com o avanço da tecnologia, os reatores estão se tornando mais eficientes, seguros e sustentáveis, permitindo que as empresas atendam às crescentes demandas do mercado e às exigências ambientais. Neste artigo, exploraremos algumas das principais inovações tecnológicas que estão moldando o futuro dos reatores industriais.
1. Automação e Controle Avançado
A automação é uma das inovações mais significativas nos reatores industriais. Sistemas de controle avançados permitem que os operadores monitorem e ajustem as condições de operação em tempo real, garantindo que as reações ocorram nas condições ideais. Isso não apenas melhora a eficiência do processo, mas também aumenta a segurança, reduzindo o risco de falhas operacionais.
Os sistemas de automação modernos utilizam sensores e dispositivos de medição para coletar dados sobre temperatura, pressão, vazão e composição química. Esses dados são analisados por algoritmos que podem prever o comportamento do sistema e fazer ajustes automáticos, otimizando a produção. A automação também permite a integração de reatores com outros sistemas industriais, como evaporadores industriais, criando uma operação mais coesa e eficiente.
2. Reatores de Fluxo Contínuo
Os reatores de fluxo contínuo têm ganhado destaque nas inovações tecnológicas, especialmente em processos que exigem produção em larga escala. Esses reatores permitem a entrada constante de reagentes e a saída contínua de produtos, aumentando a eficiência e reduzindo o tempo de ciclo. A tecnologia de reatores de fluxo contínuo é particularmente vantajosa em indústrias como a petroquímica e a produção de biocombustíveis.
Além disso, os reatores de fluxo contínuo podem ser projetados para operar em condições extremas, como altas pressões e temperaturas, o que os torna ideais para reações que exigem controle rigoroso. Essa capacidade de operar continuamente e sob condições desafiadoras resulta em uma produção mais eficiente e econômica.
3. Reatores com Catalisadores Avançados
A utilização de catalisadores avançados é outra inovação importante nos reatores industriais. Os catalisadores desempenham um papel crucial na aceleração das reações químicas, permitindo que processos ocorram em condições mais brandas e com maior seletividade. Com o desenvolvimento de novos materiais e tecnologias de síntese, os catalisadores estão se tornando mais eficientes e duráveis.
Os catalisadores avançados podem ser projetados para atuar em reações específicas, minimizando a formação de subprodutos indesejados e aumentando a pureza dos produtos finais. Essa inovação não apenas melhora a eficiência do processo, mas também contribui para a sustentabilidade, reduzindo o desperdício de recursos e a geração de resíduos.
4. Reatores Inteligentes
A tecnologia de reatores inteligentes está emergindo como uma tendência significativa na indústria. Esses reatores são equipados com sistemas de monitoramento e controle que utilizam inteligência artificial e aprendizado de máquina para otimizar as condições de operação. A capacidade de aprender com dados históricos e ajustar automaticamente os parâmetros de operação permite que os reatores inteligentes maximizem a eficiência e a segurança.
Além disso, os reatores inteligentes podem prever falhas e problemas operacionais antes que eles ocorram, permitindo que as empresas realizem manutenções preventivas e evitem paradas inesperadas. Essa abordagem proativa não apenas melhora a eficiência operacional, mas também reduz os custos de manutenção e aumenta a vida útil dos equipamentos.
5. Sustentabilidade e Processos Ecológicos
A sustentabilidade é uma preocupação crescente na indústria, e as inovações tecnológicas em reatores industriais estão se concentrando em processos mais ecológicos. Isso inclui a utilização de matérias-primas renováveis, a redução do consumo de energia e a minimização da geração de resíduos. Os reatores modernos estão sendo projetados para operar de maneira mais limpa e eficiente, atendendo às exigências ambientais e às expectativas dos consumidores.
Além disso, a implementação de tecnologias de captura e reutilização de carbono em reatores industriais está se tornando uma realidade. Essas tecnologias permitem que as emissões de CO2 sejam capturadas e reutilizadas em processos químicos, contribuindo para a redução do impacto ambiental e promovendo a economia circular.
6. Integração com Tecnologias de Indústria 4.0
A integração dos reatores industriais com as tecnologias da Indústria 4.0 está revolucionando a forma como as empresas operam. A conectividade e a troca de dados em tempo real entre diferentes sistemas e equipamentos permitem uma gestão mais eficiente e informada dos processos. Isso inclui a utilização de big data e análise preditiva para otimizar a produção e melhorar a tomada de decisões.
Com a Indústria 4.0, os reatores industriais podem ser monitorados e controlados remotamente, permitindo que os operadores acessem informações críticas de qualquer lugar. Essa conectividade não apenas melhora a eficiência, mas também aumenta a segurança, permitindo uma resposta rápida a situações de emergência.
Em resumo, as inovações tecnológicas em reatores industriais estão transformando a forma como as empresas operam, aumentando a eficiência, a segurança e a sustentabilidade. A automação, os reatores de fluxo contínuo, os catalisadores avançados, os reatores inteligentes, a sustentabilidade e a integração com a Indústria 4.0 são algumas das principais tendências que estão moldando o futuro dos reatores industriais. À medida que a tecnologia continua a evoluir, espera-se que essas inovações desempenhem um papel ainda mais importante na indústria, permitindo que as empresas atendam às crescentes demandas do mercado de forma responsável e eficiente.
Em conclusão, os reatores industriais são componentes essenciais na cadeia produtiva, permitindo a transformação eficiente e segura de matérias-primas em produtos químicos e outros materiais. A diversidade de tipos de reatores, suas vantagens operacionais, a importância da manutenção adequada e as inovações tecnológicas em curso são fatores que contribuem para a evolução contínua da indústria. À medida que as demandas do mercado e as preocupações ambientais aumentam, a adoção de tecnologias avançadas e práticas sustentáveis se torna cada vez mais crucial. Investir em reatores industriais modernos e em sua manutenção não apenas garante a eficiência e a segurança dos processos, mas também posiciona as empresas de forma competitiva em um cenário industrial em constante mudança.
Gostou? compartilhe!