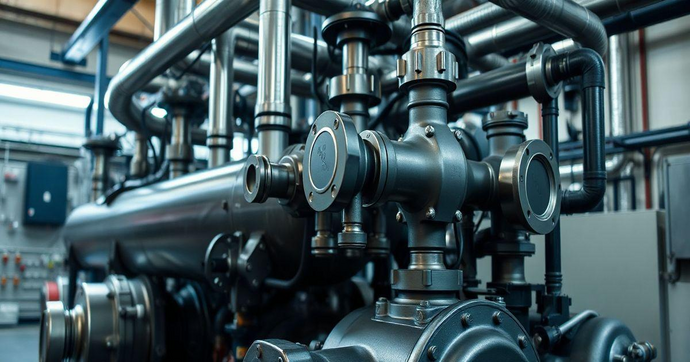
Saiba sobre Projeto de Trocador de Calor: Guia Completo e Prático
O projeto de trocador de calor é fundamental para garantir a eficiência energética em processos industriais. Esses equipamentos desempenham um papel crucial na transferência de calor entre fluidos, otimizando o consumo de energia. Neste artigo, abordaremos as etapas essenciais para o desenvolvimento de um projeto eficaz, desde os princípios de funcionamento até aplicações práticas. Continue lendo para descobrir como implementar um projeto de trocador de calor que atenda às suas necessidades específicas.
Importância do Projeto de Trocador de Calor
O projeto de trocador de calor é um passo crucial no desenvolvimento de sistemas térmicos eficientes, especialmente em indústrias que dependem da troca de calor para otimizar processos produtivos. Esses equipamentos são utilizados em diversas aplicações, incluindo aquecimento, resfriamento, condensação e vaporização de fluidos. Compreender a importância de um projeto bem estruturado é essencial para alcançar eficiência energética e reduzir custos operacionais.
A principal função de um trocador de calor é transferir energia térmica de um fluido para outro, o que transforma processos que poderiam ser custosos e ineficientes em operações mais sustentáveis e econômicas. Um projeto adequado considera diversos fatores, como a seleção de materiais, o tamanho, a configuração e a manutenção do equipamento, garantindo que ele funcione em plena capacidade e com baixa perda de energia.
Além disso, um projeto bem executado promove a segurança operacional. Trocadores de calor que não são projetados de acordo com os requisitos específicos da aplicação podem resultar em falhas, vazamentos e, em situações extremas, até acidentes. Por isso, é vital que empresas que atuam nesse setor busquem profissionais qualificados e empresas de caldeiraria especializadas para garantir um projeto que atenda todos os padrões de segurança e eficiência.
Um benefício significativo de um bom projeto de trocador de calor é a eficiência energética. O uso adequado do calor residual pode reduzir drasticamente o consumo de energia em uma fábrica, o que, por sua vez, diminui os custos com energia elétrica. Isso é especialmente relevante em um cenário onde os preços da energia estão em constante aumento e a pressão social e econômica para reduzir a emissão de carbono é maior do que nunca.
Além da eficiência energética, os projetos de trocadores de calor também impactam diretamente a sustentabilidade das operações. Com a crescente conscientização ambiental, as indústrias estão se voltando para tecnologias que minimizam a poluição e desperdícios. Um projeto bem planejado de trocador de calor permite que as indústrias utilizem recursos de maneira mais eficaz, o que contribui para uma operação mais verde e sustentável.
Outro aspecto a ser considerado é a flexibilidade que um projeto de trocador de calor pode proporcionar. À medida que as demandas de produção mudam, é fundamental que as soluções térmicas sejam adaptáveis. Um projeto que leva em conta essas variações permite modificações no sistema sem a necessidade de um investimento significativo em novos equipamentos. Isso não apenas economiza recursos, mas também facilita a resposta a novas demandas do mercado.
Por fim, não podemos esquecer a importância da manutenção que vem embutida num projeto de trocador de calor. Um projeto bem elaborado inclui planos de manutenção preventiva e preditiva, que são essenciais para garantir a longevidade do equipamento e a sua eficiência contínua. Trocadores de calor que não são mantidos adequadamente podem desenvolver problemas como incrustações ou corrosão, levando a uma redução significativa do desempenho e, consequentemente, a uma elevação dos custos operacionais.
Em resumo, o projeto de trocador de calor é um tema que não deve ser subestimado pelas indústrias. A sua importância vai além da simples funcionalidade — abrange temas como eficiência energética, segurança, sustentabilidade, flexibilidade e manutenção. Investir em um bom projeto é, portanto, um investimento em um futuro mais sustentável e lucrativo para qualquer operação industrial.
Tipos de Trocadores de Calor
Os trocadores de calor são equipamentos essenciais em diversos processos industriais e sua classificação pode ser feita com base em diferentes critérios, como o método de troca de calor, o tipo de fluido utilizado e a sua construção. Entender os diferentes tipos de trocadores de calor é crucial para selecionar o equipamento adequado para cada aplicação. Neste artigo, discutiremos os principais tipos de trocadores de calor e suas características.
Um dos tipos mais comuns de trocadores de calor é o trocador de calor de casco e tubo. Este modelo é amplamente utilizado na indústria devido à sua robustez e eficiência. Ele é composto por uma série de tubos que transportam os fluidos que vão se interagir térmicamente. Um dos fluidos percorre o interior dos tubos enquanto o outro flui ao redor deles, no espaço entre o tubo e o casco. Essa configuração permite que o trocador de calor tenha uma grande área de superfície para a troca de calor, o que é fundamental para aplicações que requerem altos níveis de transferência térmica.
Outro tipo bastante utilizado é o trocador de calor de placas. Neste modelo, as superfícies de troca de calor são formadas por uma série de placas metálicas empilhadas e fixadas em um quadro. Os fluidos são direcionados para lados opostos, passando entre as placas, onde ocorre a transferência de calor. Os trocadores de placas são conhecidos por sua alta eficiência, compactação e fácil manutenção, sendo ideais para aplicações em que o espaço é limitado. Além disso, esse tipo de trocador é facilmente expansível, o que permite adaptações futuras conforme a demanda de produção.
Os trocadores de calor ar-ar e ar-água são amplamente utilizados nos sistemas de ventilação e climatização. No caso do trocador de calor ar-ar, a troca de calor acontece entre dois fluxos de ar, o que é muito utilizado em sistemas de aquecimento, ventilação e ar-condicionado (HVAC). Já o trocador ar-água utiliza água como meio de transferência de calor, sendo comum em edifícios comerciais e industriais, onde uma maior eficiência térmica é necessária para climatização.
Os trocadores de calor de tubo duplo também merecem destaque. Eles são construídos com um tubo que contém outro tubo dentro dele. Assim, dois fluidos distintos circulam; um no espaço interior do tubo e outro no espaço entre os tubos. Este modelo é simples e de fácil fabricação, embora tenha um desempenho térmico inferior em comparação a outros tipos, como o casco e tubo. No entanto, é uma opção prática para aplicações onde a eficiência não é o fator mais crítico.
Adicionalmente, temos o trocador de calor reversível, que pode atuar em duas direções, permitindo que a troca de calor ocorra de formas diferentes conforme a necessidade. Isso é especialmente útil em processos que requerem flexibilidade operacional. Por exemplo, pode ser utilizado para aquecer ou resfriar um fluido ao longo do funcionamento da máquina.
Os trocadores de calor de fin são outra variação comum em particular para aplicações em sistemas de aquecimento. Eles empregam aletas ou "fins" para aumentar a área de superfície disponível para a troca de calor. Esta tecnologia é ideal para melhorar a eficiência de sistemas como os resfriadores industriais, onde maximizar a área de contato entre os fluidos é essencial para um desempenho ótimo.
Por último, é importante considerar os trocadores de calor de camada fina. Esses modelos são projetados para processos em que as mudanças de temperatura precisam ocorrer de forma extremamente rápida e eficiente. Geralmente, eles são encontrados em processos químicos ou quando se trabalha com fluidos que possuem propriedades específicas que exigem equipamentos delicados para uma troca efetiva de calor.
Em resumo, os tipos de trocadores de calor variam amplamente, cada qual adequado a diferentes necessidades e aplicações. A escolha do tipo certo depende de fatores como a natureza dos fluidos, a temperatura e pressão de operação e o espaço disponível. Compreender as diversas opções de trocadores de calor torna-se um ponto essencial para engenheiros e profissionais da área, garantindo que a solução escolhida atenda às necessidades específicas da aplicação industrial e maximize a eficiência energética do sistema.
Princípios de Funcionamento
Os trocadores de calor são dispositivos que transferem calor de um fluido para outro, desempenhando um papel vital em muitos processos industriais e aplicações de engenharia. Compreender os princípios de funcionamento destes equipamentos é essencial para a sua correta implementação e operação. Neste artigo, discutiremos como os trocadores de calor funcionam e quais são os mecanismos que possibilitam a troca de calor entre os fluidos.
A operação básica de um trocador de calor baseia-se na segunda lei da termodinâmica, que afirma que o calor flui naturalmente de um corpo mais quente para um corpo mais frio. Isso significa que, em um trocador de calor, sempre há um fluido que está a uma temperatura mais alta (calor) sendo transferido para um fluido a uma temperatura mais baixa (frio). Este processo de transferência térmica pode ser realizado de diversas maneiras, dependendo do tipo de trocador de calor utilizado.
Um dos principais fatores a se considerar no funcionamento de um trocador de calor é a área de superfície disponível para a troca de calor. Quanto maior a área de superfície em contato entre os dois fluidos, mais eficiente será a transferência térmica. Assim, muitos designs de trocadores de calor, como o modelo de casco e tubo ou o de placas, buscam maximizar essa área. Nos trocadores de calor de placas, por exemplo, múltiplas superfícies de troca são organizadas em uma configuração que melhora significativamente a eficiência da transferência de calor.
Outro princípio importante é a circulação dos fluidos. Um fluxo de fluido quente e um fluxo de fluido frio devem se mover simultaneamente através do trocador, e a forma como esses fluidos fluem pode afetar a eficiência da troca de calor. Em um trocador de calor de fluxo paralelo, os dois fluidos se movem na mesma direção. Embora esse método seja simples, frequentemente resulta em uma menor eficiência térmica. Por outro lado, em um sistema de fluxo cruzado ou contracorrente, os fluidos se movem em direções opostas, o que maximiza a diferença de temperatura entre eles e resulta em uma troca de calor mais eficaz.
Os trocadores de calor também podem operar seguindo ciclos de resfriamento e aquecimento, dependendo da necessidade do processo. Por exemplo, num resfriador de ar industrial, o fluido refrigerante pode ser utilizado para dissipar calor em um sistema que precisa ser mantido em uma faixa de temperatura específica. O funcionamento contínuo desses sistemas garante que a superfície de trabalho permaneça dentro dos limites de temperatura desejados.
Além da dinâmica da fluidez, a natureza dos fluidos envolvidos na troca térmica também é crucial. Os fluidos podem ser líquidos ou gases, e suas propriedades térmicas — como temperatura, viscosidade, capacidade calorífica e condutividade térmica — influenciam a eficiência da troca de calor. Por exemplo, a capacidade calorífica de um fluido determina quantos joules de energia ele pode absorver ou liberar durante a troca térmica, afetando diretamente a rapidez com que um sistema pode atingir o equilíbrio térmico.
Outro aspecto relevante é a resistência ao fluxo e à troca de calor, que pode ser causada pela presença de depósitos, incrustações e corrosão nas superfícies de troca. Manter um bom estado de limpeza e integridade do trocador de calor é vital para garantir que a troca de calor ocorra de forma eficiente e segura. A manutenção periódica e a inspeção dos trocadores de calor são práticas recomendadas para manter a eficiência e prolongar a vida útil do equipamento.
Além disso, o controle da temperatura e da pressão dentro e fora do trocador de calor é fundamental para a eficiência do sistema. Termostatos e sensores de pressão permitem o monitoramento contínuo das condições operacionais, possibilitando ajustes em tempo real que garantem uma operação otimizada e segura.
Em suma, os princípios de funcionamento dos trocadores de calor são baseados em conceitos fundamentais da termodinâmica e fluido-dinâmica. Essencialmente, eles capturam a transferência de calor entre fluidos em diferentes temperaturas, economizando energia e melhorando a eficiência em processos industriais. A escolha do tipo de trocador de calor, a configuração dos fluxos de fluidos e a manutenção adequada são fatores que impactam diretamente na eficácia e na durabilidade do sistema. Compreender esses princípios é essencial para engenheiros e profissionais da área, garantindo que sejam tomadas decisões informadas na implementação e operação desses sistemas críticos.
Etapas do Projeto de Trocador de Calor
O projeto de um trocador de calor é um processo meticuloso que envolve várias etapas cruciais para garantir a eficiência, segurança e funcionalidade do equipamento. Cada etapa deve ser realizada com atenção aos detalhes e baseia-se em princípios de engenharia térmica e de fluidos. Neste artigo, discutiremos as principais etapas envolvidas no projeto de trocadores de calor, permitindo um entendimento abrangente do processo.
A primeira etapa do projeto é a definição dos requisitos. Nessa fase inicial, os engenheiros devem identificar as especificações necessárias para o trocador de calor, considerando fatores como a temperatura e a pressão dos fluidos envolvidos, a natureza dos fluidos (líquidos ou gases), as taxas de fluxo e os níveis de eficiência térmica desejados. É fundamental que todos os parâmetros necessários sejam claramente definidos para que o projeto possa atender adequadamente às necessidades do sistema.
Após definir os requisitos, a próxima etapa é a seleção do tipo de trocador de calor. Com base nas especificações, os engenheiros precisam escolher o modelo mais apropriado. Existem diversas opções, como o trocador de calor tubular, trocadores de calor de placas e de casco e tubos, cada um com suas vantagens e desvantagens dependendo da aplicação. A escolha do tipo correto garantirá não só a eficiência na troca de calor, mas também a versatilidade e a facilidade de manutenção do equipamento a longo prazo.
A terceira etapa é o dimensionamento do trocador de calor. Nesta fase, os engenheiros realizam cálculos rigorosos para determinar o tamanho adequado do equipamento, levando em conta a área de superfície necessária para a troca de calor. Isso é feito com base nas taxas de transferência de calor e nas propriedades térmicas dos fluidos. O dimensionamento deve garantir que o trocador funcione eficientemente dentro dos limites de operação especificados. Os métodos de cálculo podem incluir a utilização de softwares especializados que auxiliam no processo de simulação e design.
A quarta etapa envolve a análise termodinâmica. Nessa fase, é realizado um estudo detalhado das condições térmicas e de pressão ao longo do trocador de calor. Este passo é crucial para identificar possíveis perdas de calor, eficiência do sistema e otimizações que podem ser feitas no projeto. A análise termodinâmica pode incluir estudos de contracorrente e fluxo paralelo, além de simulações que ajudem a prever o desempenho do trocador sob diferentes condições operacionais.
Após a análise termodinâmica, a quinta etapa é o design mecânico do trocador de calor. Essa fase compreende a criação dos desenhos técnicos e especificações mecânicas do equipamento. Os materiais a serem utilizados precisam ser selecionados com base nas condições de operação, como temperatura e pressão, além da corrosividade dos fluidos. O design deve considerar também fatores como resistência estrutural e facilidade de montagem e manutenção. Neste estágio, a colaboração entre engenheiros de diferentes especialidades, como mecânica e térmica, é vital para garantir que todos os aspectos do projeto sejam atendidos.
A sexta etapa envolve a fabricação e montagem do trocador de calor. Neste momento, os desenhos e especificações são passados para a produção, onde o equipamento é fisicamente construído. É crucial garantir que todas as etapas de fabricação sejam realizadas de acordo com os padrões de qualidade e segurança estabelecidos. Uma montagem adequada é essencial para evitar problemas futuros, como vazamentos e falhas estruturais. Inspeções e testes durante o processo de fabricação ajudam a garantir que o produto final atende às especificações desejadas.
A sétima etapa é a instalação do trocador de calor. Uma instalação correta é fundamental para garantir que o equipamento operará conforme o projetado. Os engenheiros e técnicos responsáveis pela instalação devem seguir rigorosamente as orientações do projeto, assegurando as conexões corretas e que todos os sistemas auxiliares, como controle de temperatura e pressão, estejam interligados de forma adequada. Além disso, a equipe deve realizar testes pré-operacionais para verificar se o trocador está funcionando corretamente antes de ser colocado em operação.
A oitava e última etapa é a manutenção e monitoramento. Após a instalação e a inicialização do trocador de calor, a manutenção contínua é essencial para assegurar a sua eficiência e longevidade. Isso inclui a realização de inspeções regulares, limpeza das superfícies de troca de calor e monitoramento das condições operacionais. A manutenção preventiva ajuda a detectar problemas antes que se tornem críticos, evitando paradas inesperadas e aumentando a vida útil do equipamento.
Em resumo, o projeto de um trocador de calor é um processo complexo que envolve várias etapas interligadas. Desde a definição dos requisitos até a manutenção, cada fase é crucial para garantir que o equipamento funcione de maneira eficiente e segura. A colaboração entre diferentes disciplinas de engenharia, aliada a um planejamento rigoroso, assegura o sucesso do projeto e a eficiência do sistema térmico industrial. Compreender essas etapas permite que profissionais do setor implementem soluções que atendam às demandas específicas de suas operações.
Materiais Utilizados em Trocadores de Calor
Os materiais utilizados em trocadores de calor desempenham um papel crucial na eficiência e durabilidade desses equipamentos. A escolha correta dos materiais pode impactar diretamente na transferência de calor, resistência à corrosão, capacidade de suportar pressões e temperaturas elevadas, e, consequentemente, na performance e longevidade do equipamento. Neste artigo, exploraremos os principais tipos de materiais empregados em trocadores de calor e suas características.
Um dos materiais mais comuns utilizados na fabricação de trocadores de calor é o aço carbono. O aço carbono é amplamente escolhido devido à sua alta resistência mecânica e à sua capacidade de suportar altas temperaturas e pressões. É um material econômico, o que o torna uma opção viável para muitas aplicações. No entanto, o aço carbono tem uma desvantagem significativa: ele é suscetível à corrosão, especialmente quando exposto a fluidos corrosivos. Por isso, em muitos casos, é necessário aplicar revestimentos protetores ou optar por materiais alternativos quando a corrosão é uma preocupação.
Um material alternativo ao aço carbono é o aço inoxidável. O aço inoxidável é conhecido por sua excelente resistência à corrosão, o que o torna ideal para aplicações onde há contato com fluidos agressivos. É frequentemente utilizado em indústrias químicas, petroquímicas e alimentícias, onde a proteção contra a corrosão é crucial. Além disso, o aço inoxidável possui boas propriedades térmicas, permitindo uma transferência de calor eficiente. No entanto, seu custo é geralmente mais elevado em comparação ao aço carbono.
Outro material que merece destaque é o cobre. O cobre é altamente eficiente na condução de calor e, por isso, é muitas vezes utilizado em trocadores de calor onde a eficiência térmica é a prioridade máxima. Devido à sua excelente condutividade térmica, o cobre é uma escolha popular em trocadores de calor de placas e pequenos sistemas de aquecimento e resfriamento. Contudo, o cobre é mais suscetível à corrosão do que o aço inoxidável e, portanto, seu uso é geralmente restrito a ambientes controlados ou com fluidos menos agressivos.
Além do cobre, o ligas de cobre também são utilizados em algumas aplicações. Essas ligas podem melhorar as propriedades mecânicas e a resistência à corrosão do cobre puro, tornando-as mais adequadas para certos ambientes. Exemplos comuns de ligas de cobre incluem o latão e o bronze, que são utilizados em uma variedade de aplicações em trocadores de calor, especialmente onde a resistência à corrosão e a resistência mecânica são necessárias.
As aplicações offshore e em ambientes marinhos costumam exigir o uso de materiais corroídos devido à alta salinidade e presença de água do mar. Materiais como titânio e ligas de titânio são altamente resistentes à corrosão e capacidade de suportar temperaturas elevadas, tornando-os ideais para essas condições extremas. Embora sejam mais caros, suas propriedades de resistência à corrosão e à fadiga em ambientes difíceis frequentemente justificam o investimento.
Outro material que tem ganhado popularidade em aplicações específicas de trocadores de calor é o plástico de engenharia, como o polipropileno e o PVC. Esses materiais são utilizados principalmente em trocadores de calor que lidam com produtos químicos corrosivos. A principal vantagem dos plásticos de engenharia é a sua resistência à corrosão, leveza e baixo custo, embora sua capacidade de condução térmica seja inferior à dos metais. Os trocadores de calor fabricados com esses materiais são frequentemente encontrados em processos de tratamento de água e em indústrias químicas.
Em projetos que necessitam de uma maior eficiência térmica, os materiais compósitos estão se tornando uma alternativa viável. Esses materiais são feitos combinando fibras de reforço com resinas, resultando em uma estrutura leve e resistente. Os compósitos podem ser projetados para suportar altas temperaturas e ambientes corrosivos, tornando-os uma escolha atraente para inovadores em tecnologia de trocadores de calor.
Por fim, é importante mencionar que os materiais de isolamento também são uma parte crucial da construção de trocadores de calor. O isolamento adequado minimiza a perda de calor e aumenta a eficiência operacional do equipamento. Materiais como lã de rocha, lã de vidro e espuma de poliuretano são frequentemente utilizados para esse fim, proporcionando proteção térmica e acústica.
Em resumo, a escolha dos materiais utilizados em trocadores de calor é um fator determinante para a eficiência e durabilidade do equipamento. A seleção deve ser baseada nas condições de operação, tipos de fluidos envolvidos, bem como nos requisitos de resistência à corrosão e transferência de calor. Compreender as propriedades e limitações de cada material permite que engenheiros e profissionais da área tomem decisões informadas ao projetar e implementar trocadores de calor que atendam às suas necessidades específicas.
Dimensionamento e Cálculos Necessários
O dimensionamento e os cálculos necessários para a construção de um trocador de calor são etapas críticas no projeto desse equipamento. Essas etapas garantem que o trocador funcione de forma eficiente, atenda às demandas de processo e opere dentro das especificações de segurança. Neste artigo, discutiremos os principais aspectos do dimensionamento de trocadores de calor e os cálculos essenciais que precisam ser realizados.
A primeira etapa no dimensionamento de um trocador de calor é a definição dos parâmetros operacionais. Isso inclui a identificação dos fluidos que irão passar pelo trocador, suas propriedades térmicas, temperaturas de entrada e saída, assim como as taxas de fluxo. Esses dados iniciais são cruciais, pois permitem determinar a quantidade de calor que precisa ser transferida e, consequentemente, calcular a área de superfície necessária para a troca de calor.
Um dos métodos mais utilizados para calcular a área de troca de calor é a equação de transferência de calor, também conhecida como a lei de Fourier. Esta equação é expressa da seguinte forma:
Q = U × A × ΔT
onde:
- Q = taxa de transferência de calor (kW ou BTU/h)
- U = coeficiente global de transferência de calor (W/m²·°C ou BTU/h·ft²·°F)
- A = área de superfície de troca de calor (m² ou ft²)
- ΔT = diferença de temperatura média entre os fluidos, que é comumente calculada através do método de diferença de temperatura logarítmica (DTLM).
O coeficiente de transferência de calor global (U) é um fator importante a ser considerado. Ele é influenciado pela condutividade térmica dos materiais do trocador, o tipo de fluido, suas taxas de fluxo e as condições de operação. Para calcular U, é necessário considerar as resistências térmicas ao fluxo de calor, que incluem a resistência convectiva e a resistência condutiva das paredes do trocador, além da resistência do lado do fluido. Essas resistências podem ser expressas da seguinte forma:
1/U = 1/h₁ + R_w + 1/h₂
onde:
- h₁ = coeficiente de transferência de calor do fluido quente
- R_w = resistência térmica da parede do trocador de calor
- h₂ = coeficiente de transferência de calor do fluido frio
Uma vez disposto a área de troca de calor (A), o próximo passo é determinar as dimensões do trocador de calor. Dependendo do tipo de trocador, como o trocador de calor tubular ou o de placas, as dimensões específicas (como diâmetro, comprimento e número de tubos) devem ser calculadas. Para trocadores de calor de tubos, é comum usar a equação abaixo para determinar o número de tubos necessários:
N = A / (π × D × L)
onde:
- N = número de tubos
- D = diâmetro interno do tubo
- L = comprimento do tubo
Depois que o número de tubos é definido, outras características, como a configuração do arranjo dos tubos e o espaçamento entre eles, também devem ser considerados no projeto. Esses fatores são importantes para garantir um fluxo adequado e minimizar a possível obstrução nas vias de fluído.
Além disso, é essencial incluir na análise o impacto das perdas de carga no trocador de calor. As perdas de carga referem-se à redução da pressão que ocorre à medida que os fluidos fluem através do trocador de calor. Essas perdas podem ser avaliadas utilizando a equação de Darcy-Weisbach, que é expressa como:
ΔP = f × (L/D) × (ρ × v²)/2
onde:
- ΔP = perda de carga (Pa ou psi)
- f = fator de atrito (dependente do tipo de fluxo e da rugosidade do material)
- L = comprimento do tubo (m ou ft)
- D = diâmetro do tubo (m ou ft)
- ρ = densidade do fluido (kg/m³ ou lb/ft³)
- v = velocidade do fluido (m/s ou ft/s)
Compreender as perdas de carga é fundamental para garantir que o sistema esteja operando de maneira eficiente e para dimensionar adequadamente as bombas que serão necessárias para manter a circulação do fluido.
Finalmente, após todas as etapas de cálculo e dimensionamento, é importante realizar uma validação do projeto. Isso pode incluir simulações computacionais de dinâmica de fluidos (CFD) para prever o desempenho no mundo real e identificar quaisquer problemas potenciais antes da fabricação do equipamento. O uso de softwares específicos para projetos de trocadores de calor também pode ajudar a otimizar o design, visando aumentar a eficiência e reduzir custos.
Em resumo, o dimensionamento e os cálculos envolvidos no projeto de trocadores de calor são fundamentais para garantir a eficácia e funcionalidade do equipamento. Cada etapa, desde a definição dos parâmetros operacionais até a validação final do projeto, é vital para o sucesso do sistema. Profissionais da área devem estar bem informados sobre esses cálculos e utilizar as ferramentas corretas para garantir que o projeto cumpra os requisitos de desempenho e segurança estabelecidos.
Manutenção e Cuidados com Trocadores de Calor
A manutenção adequada de trocadores de calor é essencial para garantir a eficiência do equipamento e prolongar sua vida útil. Esses dispositivos são fundamentais em uma variedade de processos industriais, onde a troca de calor é necessária para otimizar o desempenho e a segurança das operações. Neste artigo, abordaremos as melhores práticas de manutenção e cuidados que devem ser adotados para manter os trocadores de calor em condições ideais de funcionamento.
A primeira etapa na manutenção de um trocador de calor é a inspeção regular. A inspeção deve ser realizada periodicamente, a fim de detectar sinais de desgaste ou dano. Os técnicos devem procurar por vazamentos, corrosão, acúmulo de sujeira e incrustações nas superfícies de troca de calor. A realização de inspeções visuais e testes de pressão podem ajudar a identificar problemas antes que eles se tornem críticos e exijam reparos extensivos.
Uma das principais preocupações na manutenção de trocadores de calor é o acúmulo de depósitos ou incrustações nas áreas de troca de calor. Esse acúmulo pode reduzir significativamente a eficiência do trocador, já que atua como um isolante, impedindo a transferência eficiente de calor. Para evitar isso, os operadores devem implementar programas de limpeza regulares. Existem diferentes métodos de limpeza que podem ser utilizados, incluindo:
- Limpeza química: uso de soluções químicas para dissolver e remover depósitos.
- Limpeza mecânica: utilização de escovas ou equipamentos de jateamento para remover incrustações.
- Limpeza a vapor: aplicação de vapor para desentupir e limpar as superfícies internas dos tubos.
Além das práticas de limpeza, é crucial monitorar as condições operacionais dos trocadores de calor. Isso inclui avaliar as pressões e temperaturas de entrada e saída dos fluidos, bem como a taxa de fluxo. Anomalidades nessas condições podem ser um indicativo de problemas, como entupimentos ou falhas na bomba. Um monitoramento adequado pode auxiliar na detecção precoce de problemas, evitando paradas inesperadas e danos ao equipamento.
A manutenção preditiva é uma estratégia útil que envolve o uso de sensores e tecnologia para monitorar fatores como vibração, temperatura e pressão. Ao coletar dados em tempo real, os operadores podem prever falhas e programar trabalhos de manutenção antes que ocorram problemas significativos. isso não apenas ajuda a evitar quebras inesperadas, mas também pode reduzir custos ao aumentar a eficiência operacional.
A escolha dos materiais corretos durante a construção e manutenção do trocador de calor é igualmente importante. Materiais resistentes à corrosão, como aço inoxidável ou ligas específicas, podem ajudar a prolongar a vida útil do equipamento. Durante a substituição de componentes desgastados, é vital usar peças que atendam às especificações do fabricante para garantir a integridade do sistema.
Outro fator a ser considerado na manutenção de trocadores de calor é a gestão da temperatura e pressão de operação. Operar o trocador fora das condições críticas especificadas pode levar a falhas prematuras. Por exemplo, altas pressões podem causar estresse excessivo nas juntas e nas paredes do trocador, enquanto temperaturas inadequadas podem resultar em uma degradação dos materiais. Treinamentos periódicos para operadores são fundamentais para garantir que todos os envolvidos estejam cientes das práticas operacionais seguras.
A confiabilidade do sistema também depende do projeto do trocador de calor. Um projeto bem planejado deve levar em consideração o acesso para manutenção e limpeza. Por isso, é fundamental garantir que o equipamento esteja instalado em uma localização que permita fácil acesso a todos os componentes. Se a manutenção for realizada de forma rápida e eficiente, isso contribui para a operação geral, evitando paradas indesejadas.
Além disso, o uso de tecnologia de controle nos sistemas associados ao trocador de calor pode aumentar a eficiência e a segurança do processo. Sistemas de controle modernos oferecem funcionalidades que permitem ajustes automáticos, otimização do fluxo e monitoramento contínuo das condições. Isso não apenas melhora a eficiência, mas também reduz a probabilidade de falhas em equipamentos, contribuindo ainda mais para a durabilidade do trocador de calor.
Por último, é importante que o operador e a equipe de manutenção estejam treinados e capacitados para trabalhar com trocadores de calor. A formação contínua dos funcionários evita descuidos e garante que saibam identificar sinais de desgaste ou falha. Ter uma equipe qualificada é um dos maiores ativos para garantir a eficiência e a segurança dos trocadores de calor.
Em suma, a manutenção de trocadores de calor requer um enfoque multifacetado que inclua inspeções regulares, limpeza, monitoramento das condições operacionais e o uso de materiais e tecnologia adequados. Implementando práticas de manutenção preventivas e corretivas, os operadores podem garantir que esses equipamentos funcionem de maneira eficiente e segura, reduzindo custos e aumentando a vida útil dos trocadores de calor.
Aplicações Práticas em Indústrias
Os trocadores de calor são componentes essenciais em uma variedade de indústrias, desempenhando um papel crucial na eficiência energética e em processos térmicos. Sua capacidade de transferir calor entre dois fluidos de maneira eficaz os torna indispensáveis em várias aplicações industriais. Neste artigo, exploraremos algumas das principais aplicações práticas de trocadores de calor em diferentes setores industriais.
Uma das aplicações mais comuns de trocadores de calor é na indústria petroquímica. Nesse setor, eles são utilizados para a recuperação de calor nos processos de refino do petróleo, onde o calor gerado nas reações químicas é recuperado e reutilizado. Isso não apenas melhora a eficiência energética das operações, mas também reduz os custos operacionais e as emissões de poluentes. Os trocadores de calor são frequentemente usados em sistemas de pré-aquecimento e resfriamento de materiais, assim como em torres de destilação, onde a temperatura controlada é essencial para a separação correta dos compostos químicos.
Outra aplicação importante é na indústria de alimentos e bebidas. Trocadores de calor são utilizados em várias etapas do processamento, como pasteurização, resfriamento e aquecimento. Por exemplo, no processo de pasteurização, o calor deve ser aplicado a alimentos líquidos para destruir microrganismos patogênicos. Os trocadores de calor de placas são frequentemente preferidos neste setor devido à sua alta eficiência em transferir calor e ocupar menos espaço. Além disso, eles ajudam a manter a qualidade dos alimentos, evitando o superaquecimento e a degradação de nutrientes.
No setor de energia, trocadores de calor desempenham um papel fundamental em usinas térmicas e hidroelétricas. Nestas aplicações, eles são usados para otimizar a geração de energia, transferindo calor entre os fluidos de trabalho e os sistemas de resfriamento. Nos sistemas de ciclo combinado, os trocadores de calor são utilizados para recuperar calor residual dos gases de exaustão da turbina a gás, convertendo-o em energia adicional através de uma turbina a vapor. Esta abordagem contribui para uma maior eficiência do sistema e redução do consumo de combustível.
Além disso, na indústria química, os trocadores de calor são vitais para a realização de reações controladas, onde as temperaturas precisam ser mantidas em níveis específicos. Eles são utilizados em reatores químicos, onde o calor gerado ou absorvido durante a reação química deve ser cuidadosamente gerenciado. Um bom controle térmico é essencial para a segurança do processo e para garantir a formação do produto desejado em rendimentos máximos.
Na indústria farmacêutica, a precisão e a segurança são cruciais. Trocadores de calor são usados em diferentes etapas da produção, incluindo aquecimento, resfriamento e troca de calor em processos de remoção de solventes. Devido ao regulamento rigoroso do setor, os equipamentos devem ser projetados para permitir uma fácil validação e verificação, assegurando que a qualidade dos produtos finais não seja comprometida. Troca a quente também é utilizada para os processos de esterilização, onde a eficiência térmica é crítica.
Outra aplicação comum de trocadores de calor é na indústria automobilística, onde eles são usados em sistemas de refrigeração e aquecimento. No resfriamento de motores, os trocadores de calor desempenham um papel vital em manter a temperatura ideal de operação, evitando o superaquecimento. Além disso, eles são usados em sistemas de ar condicionado e aquecedores de cabine, melhorando o conforto dos passageiros e a eficiência do veículo.
Os trocadores de calor em sistemas HVAC (aquecimento, ventilação e ar condicionado) também são de suma importância. Eles ajudam a regular a temperatura de ambientes internos, otimizando as condições climáticas em edifícios comerciais e industriais. Eles são projetados para recuperar o calor do ar exaurido e transferi-lo para o ar fresco, proporcionando economia de energia e maior conforto térmico.
No campo da geração e tratamento de água, os trocadores de calor têm aplicações em processos de desinfecção e aquecimento de água. Em estações de tratamento de água, eles são usados para otimizar as temperaturas durante o processo de purificação, garantindo que a água tratada esteja dentro das normas de qualidade. Também são utilizados em sistemas de aquecimento de água para piscinas e instalações de aquecimento ambiental.
Além das aplicações mencionadas, os trocadores de calor são usados em vários outros setores, como a indústria de papel e celulose, a metalurgia e o processamento de resíduos. A versatilidade e eficiência desses equipamentos fazem deles uma escolha predominante em cenários onde a transferência de calor é necessária.
Em resumo, os trocadores de calor são amplamente utilizados em diversas indústrias, desempenhando um papel fundamental na eficiência energética e na otimização de processos. Desde a indústria petroquímica até a farmacêutica, eles são integrados em vários sistemas críticos que garantem o funcionamento eficiente e seguro de operações industriais. Compreender suas aplicações práticas é essencial para engenheiros e profissionais que buscam melhorar a produtividade e reduzir custos em seus setores.
Em conclusão, o projeto e a implementação de um trocador de calor desempenham um papel essencial na eficiência energética e na sustentabilidade das operações industriais. Através da compreensão de suas etapas, princípios de funcionamento e aplicações práticas, profissionais podem garantir que esses sistemas funcionem de maneira otimizada, economizando energia e reduzindo custos. A manutenção adequada, o cuidadoso dimensionamento e a escolha dos materiais certos são igualmente críticos para maximizar o desempenho e prolongar a vida útil do equipamento. Portanto, investir em um projeto de trocador de calor bem planejado não só é uma decisão inteligente, mas também uma necessidade para as indústrias que buscam melhorar suas operações e atender às crescentes demandas por eficiência e responsabilidade ambiental.
Gostou? compartilhe!