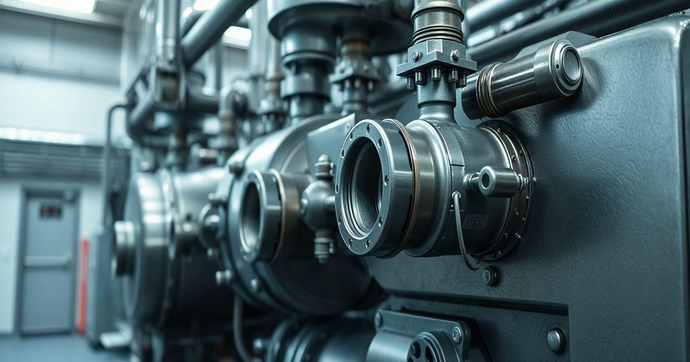
Saiba sobre Dimensionamento de Trocadores de Calor: Guia Prático
Dimensionamento de Trocadores de Calor é fundamental para garantir a eficiência de sistemas térmicos em diversas indústrias. Neste artigo, você irá aprender sobre a importância desse processo, os fatores que influenciam o dimensionamento e as técnicas adequadas para realizá-lo de forma precisa. Além disso, abordaremos os tipos de trocadores, métodos de cálculo e dicas para evitar erros comuns. Continue lendo para dominar o tema e otimizar seus projetos!
O que são Trocadores de Calor
Os trocadores de calor são dispositivos essenciais em diversas aplicações industriais, responsáveis por transferir calor entre dois ou mais fluidos. Eles operam de maneira a manter um fluido quente separado de um fluido frio, permitindo a transferência de energia térmica sem contato direto. Dessa forma, trocadores de calor desempenham um papel crucial na melhoria da eficiência energética e na otimização de processos térmicos.
Um trocador de calor básico é composto por três partes principais: as superfícies de troca térmica, os fluidos que circulam através dessas superfícies e as estruturas que suportam e dirigem o fluxo desses fluidos. A troca de calor ocorre entre os fluidos, que podem ser líquidos ou gases, e a quantidade de calor transferido depende de vários fatores, incluindo a área de troca, a temperatura dos fluidos e o coeficiente de transferência de calor.
A principal função dos trocadores de calor é transferir calor de um fluido para outro, geralmente com o intuito de aquecer ou resfriar um dos fluidos envolvidos. Por exemplo, em um sistema de refrigeração, um trocador de calor é utilizado para remover calor de um ambiente, enquanto em sistemas de aquecimento, ele pode ser empregado para aquecer água ou ar de um ambiente. Essa versatilidade torna os trocadores de calor indispensáveis em indústrias como petroquímica, química, energia, alimentos e bebidas, entre outras.
Existem vários tipos de trocadores de calor, cada um projetado para atender a diferentes necessidades e requisitos de fluxo, temperatura e pressão. Os trocadores de calor mais comuns incluem:
- Trocadores de Calor de Tubos Concêntricos: Composto por um tubo interno que transporta um fluido e outro tubo externo que transporta o fluido oposto, permitindo a troca de calor entre ambos.
- Trocadores de Calor em Placas: Composto por placas metálicas dispostas em um arranjo que aumenta a área de superfície e melhora a eficiência da troca térmica.
- Trocadores de Calor de Superfície Sólida: Utiliza superfícies sólidas para permitir a transferência de calor entre os fluidos, eficiente em aplicações específicas.
- Trocadores de Calor de Ar: Projetados para transferir calor entre um fluido e ar, frequentemente utilizados em sistemas de ventilação e aquecimento.
O dimensionamento e a escolha do tipo correto de trocador de calor são cruciais para o desempenho do sistema. Um projeto mal executado pode resultar em eficiência energética reduzida, custos operacionais mais altos e danos aos equipamentos. Portanto, é vital que engenheiros e profissionais da área compreendam as propriedades dos fluidos, as condições de operação e os requisitos de fluxo para realizar o dimensionamento adequado.
O papel das Empresas de caldeiraria no desenvolvimento de trocadores de calor é fundamental. Essas empresas são responsáveis pela fabricação e montagem de componentes que garantem alta qualidade e eficiência nos sistemas térmicos. Trabalhar com fornecedores confiáveis pode garantir não apenas a durabilidade dos equipamentos, mas também a segurança do processo industrial como um todo.
A eficiência de um trocador de calor é medida pela sua capacidade de transferir calor a uma dada taxa, considerando também a resistência ao fluxo que pode ocorrer devido ao design de seu interior. É importante observar que a eficiência de um trocador não depende apenas de seu projeto, mas também das condições de operação, como a temperatura e a pressão dos fluidos. Os trocadores de calor também podem ser classificados como recuperadores, regeneradores ou trocadores de calor de fluxo direto, cada um com seus princípios operacionais e aplicações específicas.
Na indústria, a escolha do trocador de calor ideal deve levar em consideração não apenas a eficiência térmica, mas também a facilidade de manutenção e a durabilidade do equipamento. O conhecimento sobre os diferentes tipos de trocadores e suas características pode ajudar engenheiros e operacionais a selecionar o modelo mais adequado para cada situação, resultando em um sistema mais eficiente e econômico.
Em resumo, os trocadores de calor são componentes cruciais em processos industriais, permitindo a transferência eficiente de calor entre fluidos sem mistura, contribuindo para a otimização de processos, controle de temperatura e eficiência energética. A escolha e o dimensionamento apropriados desses dispositivos são fundamentais para garantir operações industriais seguras e sustentáveis.
Importância do Dimensionamento em Trocadores de Calor
O dimensionamento em trocadores de calor é um passo crucial no processo de projeto de sistemas térmicos. Essa etapa assegura que os trocadores de calor sejam capazes de cumprir suas funções de forma eficiente, atendendo às necessidades específicas de cada aplicação. Um dimensionamento inadequado pode resultar em problemas que afetam tanto o desempenho do sistema quanto os custos operacionais. Portanto, entender a importância do dimensionamento é essencial para engenheiros, técnicos e gestores de equipes industriais.
A função primária dos trocadores de calor é transferir calor de um fluido para outro, e o dimensionamento correto é vital para garantir que essa transferência ocorra de maneira otimizada. Isso não apenas assegura a eficiência do sistema, mas também previne o desgaste prematuro dos equipamentos e reduz o consumo de energia. Um projeto bem dimensionado resultará em uma taxa de transferência de calor que está dentro dos parâmetros desejados, permitindo que o sistema opere em sua capacidade ideal.
Um dos problemas mais comuns resultantes de um dimensionamento inadequado é a sobrecarga térmica. Isso ocorre quando o trocador de calor é incapaz de remover ou adicionar calor aos fluidos nas condições de operação esperadas. Por exemplo, em um sistema de resfriamento onde um resfriador industrial não é corretamente dimensionado, os fluidos podem não atingir as temperaturas desejadas, o que compromete a eficiência de todo o processo. Isso não só influencia a qualidade do produto final, mas também pode causar falhas operacionais e aumentos nos custos de energia.
Outro aspecto crítico do dimensionamento é a questão da manutenção. Um trocador de calor que foi corretamente dimensionado tende a ser mais fácil de manter, pois opera dentro dos parâmetros projetados. Em termos práticos, isso significa que os intervalos de manutenção e os custos operacionais reduzem, aumentando a vida útil do equipamento. Equipamentos que sobrecarregam ou operam em condições extremas tendem a exigir manutenção mais frequente, resultando em paradas não planejadas e melhoria dos custos produtivos.
Além disso, o dimensionamento inadequado afeta a eficiência energética dos sistemas. Trocadores de calor subdimensionados ou superdimensionados podem levar a uma utilização intensa de energia para realizar o trabalho de troca térmica, resultando em desperdício de recursos e aumento das emissões de carbono. Em cenários industriais em que a sustentabilidade é uma preocupação crescente, o dimensionamento adequado deve ser visto como uma prioridade para minimizar o impacto ambiental das operações.
Os projetos que levam o dimensionamento em consideração também podem resultar em processos mais seguros. A operação de trocadores de calor fora das especificações de projeto pode levar a riscos de explosões, vazamentos ou falhas catastróficas. Um dimensionamento adequado contribui para manter o sistema dentro dos limites seguros de operação, garantindo a segurança dos trabalhadores e da instalação. Por essa razão, é comum que normas e regulamentos específicos exijam o dimensionamento adequado em projetos de sistemas térmicos.
Outra consequência importante do dimensionamento preciso é a possibilidade de automação dos sistemas. Em processos industriais modernos, a automação é frequentemente utilizada para aumentar a eficiência e reduzir a necessidade de intervenção humana. Para que um sistema automatizado funcione de maneira eficaz, os trocadores de calor precisam ter suas capacidades e especificidades devidamente dimensionadas. A comunicação entre sensores, atuadores e controladores é baseada nas condições ideais de operação, que só podem ser asseguradas por um dimensionamento correto.
Finalmente, é importante afirmar que o dimensionamento deve ser uma consideração inicial no desenvolvimento de qualquer sistema que utiliza trocadores de calor. Os engenheiros devem considerar não apenas as condições de operação atuais, mas também as condições potenciais futuras e as variações de carga que os sistemas poderão enfrentar. A capacidade de um trocador de calor deve ser dimensionada de acordo com uma análise abrangente da operação que permitirá a adaptabilidade e a eficiência ao longo do tempo.
Portanto, a importância do dimensionamento em trocadores de calor vai além da simples questão de eficiência térmica. Impacta diretamente a operação, segurança, custo e a sustentabilidade dos processos industriais. Investir tempo e recursos em um dimensionamento adequado é um passo estratégico que pode trazer benefícios significativos para a indústria, garantindo um retorno sobre o investimento a longo prazo. Em última análise, um trocador de calor bem dimensionado vai contribuir para operações mais inteligentes, responsivas e seguras.
Fatores a Considerar no Dimensionamento
O dimensionamento adequado de trocadores de calor é um processo complexo que requer a análise de diversos fatores interligados. Esses fatores devem ser cuidadosamente considerados para garantir que o equipamento funcione conforme as expectativas, otimizando a eficiência energética e minimizando problemas operacionais. A seguir, são destacados os principais elementos que devem ser levados em conta no dimensionamento de trocadores de calor.
Um dos primeiros aspectos a serem avaliados é a taxa de transferência de calor, que é uma das razões mais críticas para dimensionar um trocador de calor. Essa taxa determina a quantidade de calor que o equipamento precisa transferir de um fluido para outro durante o processo de operação. É fundamental calcular corretamente a carga térmica, que é influenciada pela temperatura de entrada e saída dos fluidos, bem como pelas suas propriedades físicas. Utilizar fórmulas precisas e equações de estado ajuda a prever adequadamente a transferência de calor necessária.
Temperatura de entrada e saída são outros fatores críticos. É importante entender as temperaturas em que os fluidos entram e saem do trocador de calor, pois isso impacta diretamente a eficiência do sistema. Por exemplo, se um resfriador de ar industrial não for dimensionado considerando as temperaturas corretas, a eficiência da remoção de calor será comprometida. Além disso, variações na temperatura podem ocorrer devido a diferentes condições operacionais, como flutuações na carga térmica, e isso deve ser antecipado no dimensionamento do equipamento.
Outro fator essencial a considerar é a natureza dos fluidos envolvidos no processo. A viscosidade, densidade, capacidade calorífica e condutividade térmica dos fluidos afetam a eficiência da troca de calor. É vital obter dados precisos sobre os fluidos, bem como suas propriedades durante as diferentes fases de operação. Validar essas informações é crucial, uma vez que as características dos fluidos podem variar de acordo com a temperatura e pressão, alterando a dinâmica de troca térmica.
Além disso, a configuração e design do trocador de calor devem ser estudados cuidadosamente. Existem diferentes tipos de trocadores de calor, como de tubo e placa, que têm características diversas. A escolha do tipo correto depende das exigências específicas do projeto, como espaço disponível, complexidade da instalação e aplicações industriais. Cada design terá implicações sobre a área de superfície necessária, bem como sobre a resistência ao fluxo e, consequentemente, a eficiência térmica.
A pressão de operação é outro fator que não pode ser ignorado. Trocadores de calor operam sob diferentes pressões, e o dimensionamento deve considerar as pressões de entrada e saída dos fluidos. Pressões altas podem exigir materiais específicos para garantir a integridade estrutural e a segurança do equipamento. Além disso, o dimensionamento deve incluir considerações sobre a expansão térmica e as tensões induzidas nas superfícies do trocador durante a operação.
A manutenção é também um elemento importante no dimensionamento. A facilidade de acesso para limpeza, reparos e substituições de componentes deve ser avaliada desde o planejamento. Alguns trocadores de calor são projetados com acesso fácil a partes críticas, o que facilita a manutenção preventiva. Além disso, a escolha de materiais que sejam resistentes à corrosão e ao acúmulo de depósitos irá impactar a durabilidade do equipamento e a frequência de manutenção necessária ao longo do tempo.
O contexto operacional também deve ser considerado para que se possa prever variações de carga e condições de operação. Os projetos de trocadores de calor devem ser dimensionados para suportar situações de carga mínima e máxima, garantindo que a transferência de calor ocorra de maneira eficiente em todas as circunstâncias. Isso é crucial para operações que podem ser suscetíveis a mudanças na demanda, como aquelas da indústria alimentícia ou de petroquímicas.
A normativa e regulamentação aplicável à fabricação e operação de trocadores de calor é outro fator chave. O respeito às normas de segurança e eficiência pode exigir estratégias de dimensionamento específicas, visando sempre a conformidade e segurança dos processos industriais. A integração com padrões industriais e códigos de prática reconhecidos proporciona uma maior segurança, minimizando riscos e assegurando que o projeto atenda aos requisitos de qualidade e eficiência.
Por fim, considerar o custo total de propriedade (TCO) ao dimensionar um trocador de calor é extremamente importante. Isso envolve não apenas os custos iniciais de aquisição e instalação, mas também os custos operacionais e de manutenção ao longo da vida útil do equipamento. Um projeto que considera o TCO pode levar a soluções mais rentáveis e sustentáveis, otimizando investimentos e gerenciando recursos de maneira eficaz.
Em resumo, o dimensionamento de trocadores de calor envolve uma série de fatores interligados que impactam diretamente sua eficiência e, consequentemente, a operação de processos industriais. A análise cuidadosa desses fatores garante que os trocadores funcionem dentro de seu potencial ideal, contribuindo para operações seguras, econômicas e sustentáveis. Portanto, é vital que engenheiros e técnicos estejam bem informados e capacitados para tomar decisões fundamentadas ao dimensionar esses componentes essenciais.
Tipos de Trocadores de Calor e Suas Aplicações
Os trocadores de calor são dispositivos fundamentais na troca de calor entre dois ou mais fluidos e são utilizados em uma vasta gama de aplicações em diversas indústrias. Existem diferentes tipos de trocadores de calor, cada um projetado para atender a condições específicas de operação, eficiência e requisitos técnicos. Conhecer essas variações e suas respectivas aplicações é crucial para selecionar a melhor opção para cada situação. Neste artigo, abordaremos os principais tipos de trocadores de calor e suas respectivas aplicações.
Um dos tipos mais comuns é o Trocador de calor tubular , que consiste em um conjunto de tubos onde um fluido circula dentro de tubos concêntricos, enquanto o outro fluido circula ao redor desses tubos. Este arranjo permite uma troca eficiente de calor. Os trocadores de calor tubulares são frequentemente utilizados em indústrias como a petroquímica e petroquímica, onde a resistência a altas pressões e temperaturas é necessária. Sua construção robusta também facilita a manutenção e limpeza, tornando-os ideais para aplicações que exigem serviços frequentes.
Outro tipo bastante comum é o trocador de calor em placas, que consiste em diversas placas metálicas dispostas de tal forma que formam canais para os fluidos. Esse design aumenta a área de superfície de troca térmica, resultando em alta eficiência. Os trocadores de calor em placas são frequentemente utilizados em aplicações que exigem alta eficiência de troca de calor e são frequentemente encontrados na indústria de alimentos e bebidas, em processos de pasteurização e resfriamento. Além disso, são empregados na refrigeração, aquecimento e até mesmo na indústria farmacêutica por sua flexibilidade e facilidade de limpeza.
O trocador de calor de superfície sólida opera através da transferência de calor entre superfícies sólidas e fluidos. Este tipo é comumente utilizado em aplicações que envolvem gases, onde o calor precisa ser transferido de um gás para um líquido ou vice-versa. Esses sistemas são comuns na indústria de aquecimento, onde o calor é transferido do gás combustão para a água ou outro fluido refrigerante, melhorando a eficiência e reduzindo a perda de energia.
Outro tipo a ser considerado são os trocadores de calor a ar, que permitem a troca de calor entre um fluido e o ar. Esses dispositivos são comumente usados em sistemas de aquecimento, ventilação e ar condicionado (HVAC). O projeto eficiente desses trocadores de calor é crucial para a climatização de ambientes industriais e comerciais, garantindo espaço confortável e níveis adequados de umidade. Eles também são utilizados em resfriamento evaporativo e em sistemas de recirculação de ar.
Os trocadores de calor de corrente cruzada são projetados de forma que os dois fluidos fluam em direções perpendiculares. Essa configuração permite uma boa transferência de calor em aplicações onde o espaço é limitado. Esses trocadores são frequentemente utilizados em sistemas de ventilação e exaustão, especialmente em processos que requerem troca de calor rápida. Sua versatilidade e eficiência de espaço os tornam ideais para muitas aplicações em áreas que vão desde a climatização de edifícios até processos industriais.
Os trocadores de calor de contracorrente são projetados para garantir que os fluidos fluam em direções opostas, maximizando a eficiência da transferência de calor. Esse tipo de trocador é ideal para aplicações onde os fluidos precisam ser resfriados ou aquecidos de forma precisa. Os sistemas que utilizam trocadores de calor de contracorrente são frequentemente utilizados em usinas de energia, processos químicos e na indústria de petróleo e gás, onde o controle rigoroso da temperatura é necessário.
Além desses tipos, existem também os trocadores de calor de indução, que aproveitam a circulação induzida dos fluidos para garantir uma transferência de calor mais eficiente. Esses trocadores são utilizados em aplicações onde a eficiência e o controle de temperatura são cruciais, como na indústria química, em sistemas de aquecimento e resfriamento.
A escolha do tipo adequado de trocador de calor depende não apenas das condições de operação, mas também de fatores como espaço disponível, custo e requisitos de manutenção. Além disso, o conhecimento sobre as propriedades dos fluidos e a natureza do processo ajuda a determinar qual tipo de trocador oferecerá a melhor eficiência e durabilidade ao longo do tempo.
As aplicações de trocadores de calor são vastas e podem ser encontradas em indústrias tão diversas quanto alimentícia, farmacêutica, petroquímica, geração de energia, HVAC e muitas outras. Cada tipo de trocador é projetado para atender a especificações técnicas e operacionais, garantindo que a transferência de calor seja realizada de forma eficiente e segura. A seleção criteriosa de um trocador de calor adequado pode resultar em melhorias operacionais significativas e na redução de custos de energia, tornando-se uma parte crucial do planejamento e operação de processos industriais.
Em resumo, entender os diferentes tipos de trocadores de calor e suas aplicações é essencial para otimizar sistemas térmicos em diversas indústrias. Escolher o trocador correto pode levar a uma eficiência energética aprimorada, minimizar o consumo de recursos e maximizar a produtividade das operações.
Métodos de Cálculo para Dimensionamento
O dimensionamento de trocadores de calor é um processo técnico crítico que garante a eficiência e a eficácia na transferência de calor entre fluidos. Para atingir um desempenho ideal, é necessário aplicar métodos de cálculo adequados que considerem as características específicas do sistema e os requisitos operacionais. Neste artigo, discutiremos os principais métodos de cálculo empregados no dimensionamento de trocadores de calor, suas fórmulas conforme suas aplicações e a importância de cada um.
Um dos métodos mais tradicionais e utilizados no dimensionamento de trocadores de calor é o chamado método de equilíbrio térmico. Nesse método, considera-se a quantidade de calor que deve ser transferida durante o processo. Para calcular a taxa de transferência de calor (Q), utiliza-se a fórmula:
Q = U × A × ΔT
onde Q é a taxa de transferência de calor, U é o coeficiente global de transferência de calor, A é a área de troca de calor e ΔT é a diferença de temperatura entre os dois fluidos. O coeficiente U varia dependendo do tipo de trocador de calor e das propriedades dos fluidos. Portanto, é fundamental determinar com precisão o valor de U para garantir a eficiência do sistema.
A diferença de temperatura (ΔT) pode ser um fator complexo de calcular, pois pode ser apresentada como a diferença de temperatura média (DTM) ou a diferença de temperatura logarítmica média (LMTD). A DTM é calculada na forma simples:
DTM = (T1 - T2) / ln(T1 / T2)
onde T1 e T2 são as temperaturas de entrada e saída dos fluidos em ambos os lados. A formulação correta da diferença de temperatura é essencial para um dimensionamento adequado, pois influencia diretamente na eficiência da transferência de calor.
Outro método significativo no dimensionamento de trocadores de calor é o método de efetividade-NtU. Este método é utilizado principalmente em análise de trocadores de calor de placas e tubulares. A eficácia (ε) é a razão entre a troca de calor real e a troca de calor máxima possível do trocador. Para calcular a eficácia, utiliza-se a relação:
ε = Qreal / Qmáx
O método de efetividade permite calcular a área do trocador sem precisar determinar diretamente o coeficiente de transferência de calor. Este método é especialmente útil em configurações de trocadores onde as propriedades dos fluidos variam ao longo do processo.
Para garantir precisão nos cálculos relativos à área de superfície e eficiência na transferência de calor, é importante também considerar os perfis de temperatura e os fluxos dos fluidos. Ao adotar o método de fluxo cruzado ou contracorrente, por exemplo, o desempenho do trocador pode ser otimizado. As fórmulas para análises em fluxos cruzados exigem integração dos perfis de temperatura e cálculo simultâneo das temperaturas de entrada e saída para ambos os fluidos.
Além de métodos teoréticos, o uso de softwares de dimensionamento tem se tornado cada vez mais comum. Ferramentas computacionais permitem simulações que consideram diversas variáveis ao mesmo tempo, proporcionando resultados mais completos e precisos. Esses softwares, além de simplificarem a complexidade dos cálculos, oferecem a capacidade de analisar cenários diferentes e otimizar a operação dos trocadores, levando em consideração variações em fluxo, propriedades dos fluidos e condições operacionais.
Outro aspecto importante no cálculo para dimensionamento é a consideração das resistências térmicas ao longo do processo de transferência de calor. Cada material tem uma condutividade térmica específica que afeta sua eficiência na troca de calor. Assim, as resistências térmicas devem ser somadas e incluídas nos cálculos para obter resultados mais realistas e que garantam um dimensionamento adequado. As resistências podem incluir a resistência devido à parede do tubo, forma de escala e incrustação interna.
Ademais, deve-se levar em conta as condições de operação durante o dimensionamento, uma vez que flutuações na temperatura e pressão dos fluidos podem alterar substancialmente a transferência de calor. Requisitos específicos de temperatura em processos industriais devem ser avaliados, e a variabilidade de cargas térmicas precisa ser considerada para garantir que o trocador funcione corretamente em todas as condições.
Finalmente, é essencial que os cálculos sejam validados por meio de testes práticos e medições em condições reais de operação. Embora os métodos teóricos e o uso de software sejam fundamentais, a prática pode revelar inconsistências e divergências que podem ser ajustadas durante as etapas finais do projeto e instalação. Esse processo de validação é crucial para garantir a integridade eterna da aplicação do trocador de calor ao longo do tempo.
Assim, os métodos de cálculo para o dimensionamento de trocadores de calor são variados e complexos, envolvendo abordagens teóricas e práticas. Um dimensionamento preciso é vital não apenas para garantir eficiência na transferência de calor, mas também para promover segurança e sustentabilidade nas operações industriais. Portanto, conhecimentos detalhados sobre esses métodos são essenciais para profissionais envolvidos no projeto e operação de sistemas térmicos.
Erros Comuns no Dimensionamento de Trocadores de Calor
O dimensionamento de trocadores de calor é uma etapa crucial em projetos de sistemas térmicos, onde a eficiência e a segurança operacionais são essenciais. No entanto, existem muitos erros comuns que podem ocorrer nesse processo de dimensionamento, resultando em problemas de desempenho, custos elevados e até falhas catastróficas. Neste artigo, discutiremos alguns desses erros e suas consequências, além de como evitá-los.
Um dos erros mais frequentes é o subdimensionamento do trocador de calor. Isso acontece quando o equipamento é projetado para uma taxa de transferência de calor menor do que a requerida para a aplicação. O subdimensionamento pode levar a um aquecimento ou resfriamento inadequados dos fluidos, resultando em baixa eficiência do sistema e aumento no consumo de energia. Em aplicações industriais, isto pode significar a incapacidade de manter a qualidade do produto final ou até mesmo comprometer a segurança do processo. Para evitar subdimensionamento, é crucial realizar um cálculo preciso da carga térmica e considerar as variações sazonais ou operacionais que podem impactar o desempenho do sistema.
Outro erro comum é o superdimensionamento dos trocadores de calor. Para evitar problemas com o dimensionamento, alguns profissionais podem optar por projetar um trocador com capacidade excessiva, acreditando que isso garantirá uma margem de segurança. No entanto, o superdimensionamento pode resultar em ineficiências operacionais, pois o trocador pode não operar em sua capacidade ideal. Isso pode causar aumento nos custos com energia, manutenção mais frequente e problemas de controle de temperatura. A melhor prática é encontrar um equilíbrio e dimensionar corretamente o trocador de calor com base nas necessidades reais do sistema.
Um erro frequentemente observado é a negligência na análise das propriedades dos fluidos. As propriedades térmicas dos fluidos, como viscosidade, densidade, capacidade calorífica e condutividade térmica, têm um papel significativo no desempenho do trocador de calor. Ignorar a variabilidade dessas propriedades em diferentes condições de operação pode levar a resultados imprecisos nos cálculos de dimensionamento. Portanto, é vital realizar medições precisas e utilizar dados atualizados sobre as propriedades dos fluidos que serão utilizados no processo.
A especificação incorreta do coeficiente de transferência de calor é outro erro que pode impactar o resultado final do dimensionamento. O coeficiente U, responsável pela eficiência da troca de calor, pode variar dependendo do tipo de trocador e das condições operacionais. Utilizar valores padrão que não correspondem à realidade da aplicação pode levar a estimativas equivocadas na área de superfície necessária e, consequentemente, a problemas de eficiência. Investigar as condições reais e realizar testes de desempenho são essenciais para garantir a precisão do coeficiente de transferência de calor.
O não considerar as quedas de pressão durante o dimensionamento é um erro que pode comprometer seriamente a operação do trocador de calor. Cada componente do sistema apresenta uma resistência ao fluxo que causa perda de pressão. Ignorar essas perdas pode resultar em dimensionamento insuficiente da bomba ou do sistema, resultando em um fluxo inadequado e comprometendo a eficiência do trocador. Portanto, é fundamental incluir as quedas de pressão nos cálculos, garantindo que o sistema funcione conforme projetado.
A falta de planejamento para manutenção e limpeza também é uma armadilha comum no dimensionamento de trocadores de calor. Alguns projetos podem não considerar o acesso adequado ao equipamento para inspeção e manutenção. Em sistemas onde a formação de incrustações e depósitos é uma preocupação, a limpeza regular é crítica para manter a eficiência do trocador. Designers devem garantir que o trocador seja projetado para facilitar a manutenção e avaliações periódicas, evitando assim problemas futuros de manutenção.
Outro erro que deve ser evitado é o desconsiderar as condições de operação variáveis. Muitos sistemas industriais não operam sob condições constantes; variações na capacidade de carga, temperatura ou fluxo podem ocorrer frequentemente. Projetar um trocador de calor sem considerar a flexibilidade necessária para essas variações pode levar a problemas de eficiência e performance. O dimensionamento deve incluir a consideração de uma faixa de operação onde o trocador ainda funcione de forma eficaz e segura, independentemente das flutuações.
Por fim, um erro comum é a não validação dos cálculos através de testes práticos. Embora os cálculos teóricos e simulações sejam ferramentas valiosas, os testes práticos são essenciais para garantir que o sistema funcione conforme esperado nas condições reais de operação. Ignorar a necessidade de validação pode resultar em surpresas negativas após a instalação do equipamento. Portanto, é recomendável realizar testes de desempenho e ajustes conforme necessário antes de considerar que um sistema está completamente otimizado.
Em suma, evitar erros comuns no dimensionamento de trocadores de calor é essencial para garantir que o sistema funcione com eficiência e segurança. Um entendimento abrangente dos requisitos operacionais, controle rigoroso das condições de operação e a consideração de todas as variáveis envolvidas no processo são cruciais para alcançar um dimensionamento adequado. Realizar análises precisas e implementar práticas adequadas pode prevenir problemas futuros, economizar custos e assegurar a longevidade do sistema de troca térmica.
Manutenção e Otimização de Trocadores de Calor
A manutenção e otimização de trocadores de calor são aspectos fundamentais para garantir a eficiência e a durabilidade desses componentes cruciais em sistemas térmicos. Esses dispositivos, utilizados em uma variedade de aplicações industriais, desempenham um papel vital na transferência de calor entre fluidos e, portanto, sua integridade e desempenho são essenciais para a operação eficiente de um sistema. Neste artigo, abordaremos as melhores práticas de manutenção e estratégias de otimização que podem ser implementadas para maximizar o desempenho dos trocadores de calor.
Uma das práticas mais importantes de manutenção é a limpeza regular dos trocadores de calor. Com o tempo, a formação de incrustações, lamínulas ou depósitos pode ocorrer nas superfícies de troca térmica, reduzindo a eficiência do processo de transferência de calor. Os depósitos, que podem resultar de impurezas ou minerais nos fluidos, aumentam a resistência térmica e, consequentemente, comprometem o desempenho do trocador. Métodos de limpeza podem incluir métodos químicos, mecânicos ou até mesmo usando água em alta pressão, dependendo da natureza dos depósitos e do tipo de trocador. Uma estratégia eficaz pode incluir a programação de limpezas regulares como parte do plano de manutenção preventiva.
Inspeções visuais também são essenciais para a manutenção de trocadores de calor. Inspecionar visualmente os equipamentos em intervalos regulares pode ajudar a identificar problemas antes que se tornem sérios. Fraturas, vazamentos, corrosão ou desgaste nas superfícies do trocador são sinais que devem ser observados cuidadosamente. A identificação precoce de problemas pode evitar falhas dispendiosas e prolongar a vida útil do equipamento. A técnica de inspeção pode ser complementada com tecnologias não destrutivas, como ultrassom ou raios-X, para um exame mais profundo.
A manutenção preditiva é uma abordagem que está ganhando popularidade por sua eficácia em prolongar a vida útil dos trocadores de calor. Essa estratégia envolve a monitoração contínua do desempenho do equipamento e o uso de dados para prever quando a manutenção é necessária. Isso pode incluir a medição de variáveis como pressão, temperatura e taxas de fluxo, permitindo a detecção de desvios que podem indicar um problema. Tecnologias avançadas, como Internet das Coisas (IoT) e análises preditivas, podem ser integradas para permitir uma abordagem mais proativa para a manutenção, reduzindo o tempo de inatividade não planejado.
A otimização do desempenho dos trocadores de calor não se limita apenas à manutenção. Envolve também a implementação de estratégias que melhorem a eficiência da troca térmica. Um dos caminhos para otimizar o desempenho é ajustar os parâmetros operacionais, como temperatura e pressão dos fluidos. Incrementos nas temperaturas de entrada podem levar a um aumento na eficiência da troca de calor, desde que os limites materiais sejam respeitados. Além disso, realizar análises de simulação pode ajudar a identificar as condições ideais de operação, permitindo que o trocador funcione em seu ponto de maior eficiência.
Outra maneira de otimizar os trocadores de calor é avaliar e reformular a configuração do fluxo. A escolha do arranjo de fluxo (contracorrente, contracorrente, cruzado, etc.) pode influenciar diretamente a eficácia do trocador. Em muitos casos, o ajuste da configuração do fluxo pode resultar em ganhos significativos na eficiência do sistema. O conhecimento sobre as condições de operação e as propriedades dos fluidos é fundamental para selecionar o arranjo mais apropriado.
A implementação de sistemas de recuperação de calor é uma estratégia eficaz para otimizar trocadores de calor em aplicações industriais. Esses sistemas aproveitam o calor residual, redirecionando-o para aquecer outros fluidos ou até mesmo para gerar energia. Ao incorporar a recuperação de calor, é possível aumentar significativamente a eficiência global do sistema, além de reduzir custos operacionais e minimizar o impacto ambiental.
A seleção adequada de materiais para os trocadores de calor também é um fator impacto na manutenção e otimização. Materiais que oferecem resistência à corrosão e ao desgaste podem aumentar a durabilidade dos trocadores e reduzir a frequência de manutenção necessária. A análise de características dos fluidos, como pH, temperatura e composição, pode orientar a escolha de materiais que garantirão o máximo desempenho e confiabilidade.
Por fim, firmar parcerias com empresas especializadas pode agregar valor significativo à operação dos trocadores de calor. A colaboração com empresas de caldeiraria e fornecedores que entendem a mecânica dos trocadores de calor pode trazer expertise em manutenção e otimização. Ter acesso à experiência de profissionais capacitados pode ajudar a construir um plano de manutenção sólido e estratégias de otimização que aumentarão a eficiência e a durabilidade do equipamento.
Em resumo, a manutenção e a otimização de trocadores de calor são cruciais para garantir um desempenho eficiente e prolongar a vida útil do equipamento. Implementar práticas regulares de limpeza e inspeção, adotar uma abordagem preditiva, otimizar condições operacionais e escolher os materiais corretos são todas estratégias fundamentais para ter sucesso nesse aspecto. Através de uma gestão proativa e informada, é possível maximizar o desempenho dos trocadores de calor, resultando em operações industriais mais eficientes e sustentáveis.
Estudos de Caso sobre Dimensionamento de Trocadores de Calor
O dimensionamento de trocadores de calor é um processo crítico que impacta diretamente a eficiência e a segurança de sistemas térmicos em diversas aplicações industriais. Para entender melhor as nuances e as melhores práticas na escolha e dimensionamento desses equipamentos, é essencial explorar casos reais. Os estudos de caso não apenas ilustram a teoria por trás do dimensionamento, mas também fornecem lições valiosas para a prática. Neste artigo, discutiremos alguns estudos de caso que demonstram o impacto do dimensionamento correto de trocadores de calor.
Um exemplo notável vem da indústria petroquímica, onde a eficiência energética é de vital importância. Em uma refinaria, um trocador de calor tubular foi projetado para maximizar a transferência de calor entre o óleo diesel e o vapor d'água. Os engenheiros realizaram um análise meticulosa das condições operacionais, incluindo as taxas de fluxo, temperaturas de entrada e saída, e as características dos fluidos. Após a construção do trocador, foi identificado que o coeficiente de transferência de calor foi superestimado, resultando em um trocador que não atendia aos requisitos de desempenho. A partir dessa experiência, a equipe revisou seu processo de seleção de coeficientes, garantindo dados mais precisos, o que levou a uma segunda iteração do projeto que atendeu perfeitamente às expectativas operacionais.
Outro estudo de caso interessante surgiu em uma fábrica de alimentos, onde um trocador de calor em placas foi empregado para resfriar água quente gerada por um processo de pasteurização. A necessidade de manter as temperaturas dentro dos padrões de segurança alimentar impulsionou os engenheiros a reavaliar o dimensionamento inicial. A análise não apenas considerou a carga térmica, mas também as variações de fluxo que ocorriam durante o processo de produção. Durante a implementação do novo projeto, eles ajustaram a área da superfície de troca de calor com base em simulações que levaram em conta a eficácia e a resistência ao fluxo. Isso resultou em um sistema que não apenas cumpriu os requisitos de temperatura, mas também reduziu os custos operacionais por meio de uma melhor eficiência energética.
Um caso emblemático na indústria química revela a importância do dimensionamento em ambientes corrosivos. Em uma planta que lidava com processos químicos agressivos, o trocador de calor foi inicialmente projetado com materiais comuns, levando a uma rápida degradação e falhas prematuras. Após uma análise de falha, a equipe decidiu implementar um trocador de calor de alta resistência, feito de ligas metálicas específicas para combater a corrosão. Esse ajuste não só aumentou a durabilidade do equipamento, mas também minimizou as paradas não planejadas, contribuindo assim para maior segurança e eficiência em toda a operação.
No contexto da indústria de energia, um estudo de caso destacou os benefícios da recuperação de calor com um trocador de calor de contracorrente. Uma usina térmica estava enfrentando o desafio de descartar calor excessivo, o que resultava em perda de eficiência. Os engenheiros projetaram um sistema de recuperação que capturava o calor residual dos gases de combustão para aquecer a água de alimentação da caldeira. Este projeto não apenas melhorou a eficiência térmica global da usina, mas também reduziu os custos de combustível e as emissões de gases. O sucesso dessa implementação demonstrou a importância do dimensionamento adequado da rede de recuperação de calor, que tinha que ser suficiente para lidar com as flutuações nas taxas de fluxo e temperatura.
Outro exemplo fascinante pode ser encontrado no setor de climatização, onde um projeto de sistema de aquecimento e resfriamento utilizando um trocador de calor de ar foi revisado após a medição de seu desempenho em ambientes operacionais. Inicialmente, o projeto foi dimensionado com base em estimativas teóricas, mas a análise do desempenho durante as primeiras semanas de operação revelou que a capacidade real não atendia as demandas de carga durante picos de temperatura. Por meio da coleta de dados e ajustes práticos, a equipe redimensionou o trocador de calor, resultando em um aumento na eficiência do sistema e prolongando a vida útil do equipamento.
A valiosa aprendizado extraída desses estudos de caso ilustra não apenas a importância do dimensionamento adequado em si, mas também as considerações mais amplas em torno de uma boa análise dos requisitos operacionais, propriedades dos fluidos e ambiente de operação. Além disso, essas experiências mostram que a comunicação entre as equipes de engenharia e operação deve ser contínua e adaptativa, permitindo ajustes que garantam a eficiência máxima do sistema.
Por fim, esses exemplos reafirmam que o dimensionamento de trocadores de calor não é um processo estático, mas que deve ser continuamente revisado e otimizado ao longo do ciclo de vida do equipamento. A experiência adquirida em casos reais de projeto e operação pode ser aplicada para melhorar continuamente os sistemas de troca de calor, promovendo não apenas eficiência, mas também segurança e sustentabilidade.
Em resumo, os estudos de caso sobre dimensionamento de trocadores de calor apresentam uma riqueza de informações que podem orientar engenheiros e profissionais em futuras implementações. Compreender os desafios enfrentados e as soluções desenvolvidas em diferentes cenários pode levar a melhores práticas e a um desempenho otimizado em sistemas térmicos em todo o setor industrial.
Em conclusão, o dimensionamento de trocadores de calor é uma etapa crucial que desempenha um papel significativo na eficiência operacional de sistemas térmicos em diversas indústrias. Ao longo deste artigo, exploramos a importância desse processo e os diversos fatores que impactam sua execução, como as características dos fluidos, as condições operacionais e as escolhas de materiais. Além disso, discutimos os diferentes tipos de trocadores de calor, métodos de cálculo eficazes e as armadilhas comuns a serem evitadas. A compreensão desses elementos é essencial para garantir não apenas a performance ideal dos trocadores, mas também a segurança e a sustentabilidade das operações. Ao aplicar as técnicas e conhecimentos abordados, você estará mais preparado para otimizar seus projetos e contribuir para a eficiência energética das suas instalações. Portanto, continue se aprofundando no tema e aplique esse conhecimento em sua prática profissional.
Gostou? compartilhe!