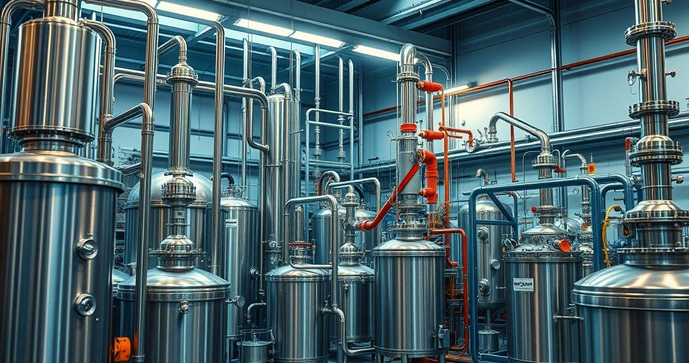
Saiba sobre Como escolher reatores químicos industriais para otimizar sua produção
Principais tipos de reatores químicos industriais disponíveis
Os reatores químicos industriais são fundamentais para várias reações químicas em larga escala. Diversos tipos de reatores estão disponíveis no mercado, cada um projetado para atender a necessidades específicas de processo e capacidade. Compreender esses tipos é crucial para otimizar a produção.
Um dos tipos mais comuns é o reator de tanque agitado. Este equipamento consiste em um tanque com um agitador interno que promove a mistura de reagentes, facilitando as reações. Ideal para reações em fase líquida, esses reatores são flexíveis e podem ser ajustados para diferentes volumes.
Outro tipo amplamente utilizado é o reator tubular, que é projetado para processos de reação contínua. Neste sistema, os reagentes fluem através de um tubo, onde a reação ocorre ao longo do caminho. Reatores tubulares são eficientes em termos de espaço e permitem um controle preciso da temperatura e da pressão.
Os reatores de leito fixo e leito fluido também são populares na indústria química. Os reatores de leito fixo têm um suporte sólido onde os catalisadores são fixados, permitindo que os gases ou líquidos passem por eles. Já os reatores de leito fluido proporcionam uma mistura contínua dos sólidos com os líquidos ou gases, favorecendo reações rápidas.
Os reatores de coluna também merecem destaque. Esse tipo é frequentemente utilizado na separação e purificação de substâncias químicas. As colunas permitem que os vapores subam enquanto os líquidos descem, otimizando a transferência de massa durante os processos.
Por fim, existem reatores semicontínuos, que combinam características de reações em lotes e contínuas. Esses reatores são ideais para produtos que requerem diferentes tempos de residência e podem ser ajustados para atender a variações na produção.
Como calcular a capacidade ideal do reator
Calcular a capacidade ideal do reator é uma etapa crucial na engenharia de processos químicos. Essa capacidade determina não apenas a quantidade de produto que pode ser gerada, mas também a eficiência e a viabilidade econômica do processo.
O primeiro passo para calcular a capacidade do reator envolve entender a reação química planejada, incluindo a estequiometria da reação. Isso significa saber a quantidade de reagentes necessária para produzir uma certa quantidade de produto. Utilizando a equação química balanceada, é possível determinar a relação entre os reagentes e os produtos.
Uma vez que a estequiometria é estabelecida, o próximo passo é considerar a taxa de conversão desejada. A taxa de conversão é a fração dos reagentes que se transforma em produtos ao final da reação. Essa porcentagem irá influenciar diretamente o volume do reator necessário, uma vez que uma taxa de conversão mais alta resultará em uma necessidade maior de espaço.
Além disso, a taxa de reação é um fator relevante. Dependendo das condições de temperatura e pressão, reações diferentes irão ocorrer a velocidades diversas. Utilizar dados cinéticos obtidos de experimentos ou literatura pode ajudar a modelar o comportamento do sistema e prever a capacidade do reator com mais precisão.
Outro aspecto a considerar é o tempo de residência, que é o tempo que os reagentes passam dentro do reator. O tempo de residência também está relacionado à taxa de conversão e à taxa de reação, e deve ser ajustado para garantir a eficiência do processo.
Para calcular a capacidade do reator em litros ou metros cúbicos, pode-se utilizar a fórmula: V = (F * τ) / X, onde V é o volume do reator, F é a taxa de alimentação ou fluxo dos reagentes, τ é o tempo de residência e X é a taxa de conversão. Esta equação fornece uma base sólida para dimensionar seu reator de acordo com as necessidades do processo.
Por fim, é importante considerar fatores adicionais, como a eficiência do misturador e as características físicas dos reagentes, que podem afetar a homogeneidade e a eficiência da reação. Uma análise cuidadosa e uma modelagem robusta são essenciais para garantir que a capacidade do reator atenda às expectativas de produção.
Materiais utilizados na fabricação de reatores químicos
A escolha dos materiais utilizados na fabricação de reatores químicos é um fator essencial que pode impactar diretamente a durabilidade, a segurança e a eficiência das operações. Diferentes reatores exigem materiais específicos, dependendo das condições de trabalho, como temperatura, pressão e a natureza dos reagentes.
Um dos materiais mais comuns é o aço carbono, que é frequentemente utilizado na construção de reatores devido à sua resistência e facilidade de fabricação. No entanto, ele pode não ser adequado para ambientes corrosivos, onde outras opções são mais apropriadas.
O aço inoxidável é uma escolha popular para reatores que lidam com produtos químicos agressivos. Este material possui excelente resistência à corrosão e oxidação, garantindo a integridade do reator ao longo do tempo. Além disso, sua facilidade de limpeza é um fator benéfico em processos que envolvem produtos farmacêuticos e alimentícios.
Outro material importante é o vidro, frequentemente utilizado em reatores de pequeno porte ou em aplicações de laboratório. O vidro permite visualizar o processo de reação e é altamente resistente a muitos produtos químicos. No entanto, sua fragilidade pode limitar seu uso em grandes reatores industriais.
Os polímeros e resinas, como o polipropileno e o PTFE, também são utilizados em aplicações especiais, especialmente onde a resistência química é necessária, mas o peso é uma preocupação. Esses materiais são frequentemente encontrados em reatores de fluxo laminar e em sistemas de processo que não exigem altas pressões e temperaturas.
Além dos materiais do corpo do reator, os componentes internos, como agitadores e suportes, também devem ser considerados. Muitas vezes, são feitos de materiais que oferecem resistência ao desgaste e à corrosão, como ligas especiais de metal ou cerâmica.
Por fim, é importante que os engenheiros de processo considerem as normas e regulamentações de segurança ao selecionar os materiais para reatores químicos. A compatibilidade do material com os reagentes, a resistência a picos de temperatura e pressão, assim como a facilidade de manutenção, desempenham um papel fundamental na eficiência e segurança do processo químico.
Requisitos de segurança na operação de reatores
A segurança na operação de reatores químicos é uma prioridade fundamental, considerando os riscos associados ao manuseio de substâncias químicas e as condições operacionais envolvidas. A implementação adequada de requisitos de segurança ajuda a prevenir acidentes e garante a integridade dos trabalhadores e do ambiente.
Um dos principais requisitos é a avaliação de risco. Antes de instalar e operar um reator, é essencial conduzir uma análise abrangente de risco para identificar perigos potenciais e estabelecer medidas de controle. Isso inclui a análise de cenários que podem levar a falhas, como vazamentos, explosões ou liberações de produtos químicos nocivos.
Os sistemas de contenção são outra medida de segurança vital. Reatores devem estar equipados com dispositivos de contenção, como diques ou sistemas de drenagem, para prevenir o vazamento de substâncias perigosas. Em caso de falha, essas medidas ajudam a conter o material químico dentro de uma área segura.
Além disso, é crucial incorporar alarmes e sistemas de monitoramento em tempo real. Esses sistemas podem fornecer alertas automáticos em caso de desvios de operação ou anomalias, permitindo que a equipe de operação tome ações corretivas imediatas para mitigar riscos.
Os dispositivos de segurança, como válvulas de alívio de pressão, também desempenham um papel importante na operação de reatores. Esses dispositivos ajudam a evitar o aumento excessivo de pressão dentro do reator, que poderia resultar em falhas estruturais catastróficas. Válvulas bem projetadas devem ser regularmente verificadas e mantidas para garantir seu funcionamento adequado.
Os dados de segurança operacional devem ser bem documentados, incluindo manuais de operação, procedimentos de emergência e protocolos de treinamento. As equipes devem receber formação regular sobre os procedimentos de segurança, e simulações de situações de emergência devem ser frequentemente realizadas para garantir que todos saibam como agir em caso de acidente.
Por fim, a manutenção regular é fundamental para garantir a segurança. Isso inclui inspeções sistemáticas do equipamento, substituição de componentes desgastados e validação das informações de segurança. Manter registros detalhados de todas as manutenções e ajustes realizados é igualmente essencial para a conformidade e a segurança contínua.
Manutenção eficaz para reatores químicos industriais
A manutenção eficaz de reatores químicos industriais é crucial para garantir a continuidade das operações, a segurança dos trabalhadores e a qualidade dos produtos. Um programa de manutenção bem estruturado ajuda a minimizar o tempo de inatividade e reduz os custos associados a reparos imprevistos.
Um dos primeiros passos para uma manutenção eficaz é estabelecer um cronograma regular para inspeções e manutenções preventivas. Isso inclui verificar todos os componentes, como válvulas, bombas, sensores e sistemas de controle, para identificar desgastes ou falhas antes que se tornem um problema sério.
As inspeções visuais desempenham um papel fundamental na manutenção. Operadores devem ser treinados para reconhecer sinais de desgaste, corrosão ou vazamentos que podem indicar a necessidade de manutenção adicional. Inspeções regulares ajudam a garantir que o reator opere de acordo com os padrões de segurança e eficiência.
Além de inspeções, a lubrificação adequada é vital para o funcionamento contínuo do equipamento. Componentes móveis, como agitadores e válvulas, devem ser lubrificados em intervalos regulares, conforme as recomendações do fabricante, para evitar atritos excessivos que podem levar a falhas prematuras.
É igualmente importante acompanhar as condições operacionais do reator. Registrando e analisando dados, como temperatura, pressão e taxas de fluxo, a equipe pode detectar padrões que indicam problemas iminentes. Ferramentas de monitoramento em tempo real são particularmente úteis para otimizar o desempenho e antecipar a necessidade de intervenções.
A implementação de um sistema de gestão de manutenção, que inclua registros detalhados de todas as atividades de manutenção realizadas, facilita a identificação de tendências e a análise de falhas. Com esses dados, é possível aprimorar continuamente os procedimentos de manutenção e reduzir os custos operacionais a longo prazo.
Por fim, a equipe envolvida na manutenção deve receber treinamento contínuo, garantindo que esteja atualizada sobre as melhores práticas e novas tecnologias. Investir em capacitação não só melhora a eficiência da manutenção, mas também aumenta a segurança no ambiente operacional.
Tendências atuais em reatores químicos e inovação
As tendências atuais em reatores químicos refletem a evolução das tecnologias de processamento e a crescente demanda por eficiência e sustentabilidade. Inovações nesse campo estão moldando a forma como os reatores são projetados, operados e integrados em processos industriais.
Uma das principais tendências é a automação e o uso de tecnologias de controle avançadas. Sistemas de monitoração em tempo real e controle automatizado permitem uma operação mais precisa e eficiente dos reatores. Isso resulta em índices de produção otimizados e minimização de erros operacionais, aumentando a segurança e a eficiência.
Além disso, a digitalização e a Indústria 4.0 têm influenciado a forma como as operações de reatores são gerenciadas. O uso de big data e análises preditivas facilita o entendimento do comportamento dos processos, permitindo ajustes em tempo real e aumentando a capacidade de resposta a falhas.
A sustentabilidade e a economia circular também estão na vanguarda das inovações em reatores químicos. Muitas indústrias estão buscando formas de reduzir o desperdício e otimizar o uso de recursos. Isso inclui o desenvolvimento de reatores que reciclavam subprodutos e outras matérias-primas, contribuindo para práticas mais ecológicas.
Os reatores modulares são outra tendência em ascensão. Essa abordagem permite que reatores sejam projetados para serem facilmente configurados e escalados de acordo com as necessidades de produção. A modularidade proporciona flexibilidade nas operações, permitindo que as empresas adaptem rapidamente suas capacidades produtivas à demanda.
A integração de novas tecnologias, como micro-reatores e reatores de fluxo contínuo, também está transformando os processos químicos. Esses sistemas são conhecidos por sua eficiência em pequenas escalas e pelo potencial para reduzir custos operacionais e melhorar o controle das reações.
Por fim, a colaboração entre academia e indústria está se intensificando, gerando inovações que atendem às necessidades do mercado. Projetos de pesquisa e desenvolvimento conjuntos estão impulsionando avanços que podem levar a processos mais eficientes e sustentáveis.
Em suma, compreender os aspectos fundamentais dos reatores químicos industriais, desde sua seleção e operação até a manutenção e inovação, é vital para maximizar a eficiência e a segurança dos processos químicos.
A escolha adequada do tipo de reator e dos materiais, juntamente com a implementação rigorosa de práticas de segurança e manutenção, asseguram que as operações sejam não apenas produtivas, mas também sustentáveis.
A adoção de novas tecnologias e tendências, como automação e digitalização, posiciona as empresas para enfrentar os desafios atuais e futuros, garantindo sua competitividade no mercado.
Investir na formação contínua das equipes e na realização de análises de risco, além de estar atento às novas inovações, permitirá que as indústrias se destaquem em um ambiente em constante mudança.
Gostou? compartilhe!